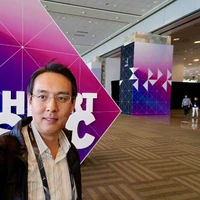
maximuslee07/llama-2-13b-rockwellautomation
Text Generation
•
Updated
•
989
•
1
text
stringlengths 36
33.4k
|
---|
<s>[INST] CompactLogix Summary: AENT Error Dear All, We are using L24ER Processor for one of our application connected with the point IO's actually we have 3 panels controlled by a single processor and the controlling mode is through ethernet(All ethernet cables are CAT6) we enabled ring supervisor mode in ETAP as well as in CPU. Now what exactly problem is during the idle condition of all panels everything is normal but once the customer starts the production the process is running good for 3 to 3.5 hours after that the HMI communication gets failed and it itself gets recover this communication failure takes place again and again in 5 - 10 mins interval.During this communication failure process din't affected it is running smoothly still yesterday but from today on during this time process also gets trip so we analysed reason for trip at that time we found that LED status of POINT BUS STATUS & NETWORK STATUS of all AENT's connected is in blinking red so please suggest what may be the problem and how can i overcome this issue NOTE 1) THIS ISSUE TAKES PLACE AFTER 3 - 3.5 HOURS FROM THE STARTING TIME 2) AS PER THE INFORMATION PROVIDED PANEL TEMPERATURE GOES TO 70-75 C AT THE TIME OF ISSUE 3) I ATTACHED THE IMAGE HOW I CONNECTED ALL THE PANEL THROUGH ETHERNET THIS IS BECOMING A SERIOUS ISSUE AT SITE IF WE ARE NOT GOING TO RECTIFY THIS PROBLEM THEN CUSTOMER WILL NOT TRUST OUR PRODUCT WE HAVE TO GIVE THEM A CORRECT SOLUTION.THE PROBLEM MAY BE FROM PANEL OR PLC OR IO'S BUT WE HAVE TO SUGGEST THE PROPER SOLUTION AS SOON AS POSSIBLE [/INST] It sounds to me like you are not providing sufficient airflow or cooling for the POINT module assemblies and they are simply overheating. 1734 POINT are rated for operation up to 55 C, which is typical for most general-purpose automation equipment. POINT I/O tends to generate quite a bit of heat, and the installation instructions (and the Knowledgebase) are very strict in their recommendations for proper module spacing and ventilation. I think you should pursue enclosure cooling or additional ventilation for this system. Thank you for your suggestions. i have a doubt that is this type of problem only takes place because of high panel temperature.if so how can i overcome this problem. Today i get a photo from a site regarding the communication issue i upload that photo for your better reference. As mentioned at previous post this problem doesn't happens at idle condition it only takes place at the time of production Is the temperature that high when the machine is not in operation ? You still should not run the system that hot or there is no reason to expect it will ever run reliably. The screenshots and pictures won't tell the whole story. You need to get online with that controller (maybe over USB) and determine the fault codes for those I/O modules. Is the ETAP module faulting as well ? Your picture shows no fault light on the controller itself, so there's no good reason for the communications between the PanelView and the CompactLogix to fail unless the communications module is failing. Do you have any diagnostic code in the CompactLogix to check for media issues on the Ethernet network ? What happens if you disconnect the PLC from the network during runtime. Is the fault LED behavior on the POINT I/O similar ? How do you recover the system ? Do you cycle power, or cool it down, or something else ? Ho ya the temperature is normal at idle condition. Actually i tried to attend the fault through remote connection so once i took the controller online unexpectedly i found 2 IO modules connected in different panels is in fault mode (Module status in module is in blinking red) controller IO is blinking in green so i checked for the fault code in IO module and the fault code id 16#031C & fault type is recoverable so i don't know reason for this code this fault code is similar for both the faulted modules so i remove the faulted IO's and changed the configuration and downloaded again so after all are smooth but still above mentioned problem are continuing I don't know about what happens when disconnecting the PLC from network during runtime Speaking about system recovery... previously only HMI communication issue takes place so at that time the user recycle the power then after it works good for some time and again starts the trouble.But from yesterday we are suffering from new problem that i mentioned in above post(1st post) Actually PLC image shown in the picture is video file but unfortunately i cannot get the file from customer once i get the video i will upload it for the reference Kakkerlak is correct - 70-75C is quite high for an internal enclosure temperature. You say this is the internal panel temperature? If the ambient temperature is lower than 70-C, then leave the enclosure doors open and see if the fault occurs. n </s> |
<s>[INST] How to sort an Array Summary: Sort an array of DINT's based on highest valueHi, I am trying to write some code to generate a 'top faults list' which can be displayed on my HMI. I am using counters to count each fault, then I map the counter.acc value out to an array of DINT's. Each element in the array is linked to a specific message, for instance fault 10 is mapped to counter 10 which is mapped to position 10 in the array. I need a way to sort the array so that I can tell which DINT has the highest value, which has the second highest and so on. I then want to use this information to trigger a fault on a Local Message list in my factory talk studio program. Are there instructions available to do this simply without having to generate loads of code? On the HMI each fault position displayed will have its own local message diaplay, I am hoping if I can figure out a way to sort the array I can use the value in the second position of the array to trigger the second local message display, and so on. Does this make sense? Has anybody any pointers? [/INST] I'm not aware of any simple method, unless somebody has written an Add On Instruction, so you'd have to do the code yourself. Sort techniques are part of any university computer science course, so I'm sure you'll find many examples (in high-level languages or pseudo-code) on the web. They vary in efficiency and coding complexity. I don't know what HMI you are using, so the following may not be useful to you; in RSView SE, using FactoryTalk Alarms and Events you can configure your alarm summary to sort on Alarm Count. The Alarm Count is generated in the PLC if you use the ALMD and ALMA instructions. Try going to the sample code webpage and searching on the term Bubble. You should get back two results. http://search.rockwellautomation.com/search?site=sample_code&client=samplecode&output=xml_no_dtd&proxystylesheet=samplecode Hi Guys, I am using FTV SE with the ALMD instructions, so the first option is the cleanest and most straight forward for me. Very simple to implement with minimal amount of code. This is my first SE project so I am just becoming familiar with its functionality. Thanks for the info TJ, the bubble sort looks useful for future reference but Factory Talk Alarms and Events solves my problem. n </s> |
<s>[INST] Flying step change I use PowerFlex 700 drive in Pos/Spd Prof mode (Speed/Torque Mod P88). The used profil has 3 steps. First : Type: Encode abs.Second : Type: Encode abs.Third : Type : End Hold Pos. This is what I want to do : I command the first step and while it is running, then I command the second one on the fly. I expect the drive decel to the speed of the second step and the second step will finish. This is what I obtain. The first Step finishes and the motor stop before restarting with the second Step. Then the third Step takes place and the drive stop. I don’t want to have this positionning between the two steps. Note: I did it with step type EncIncBlend as fist step but it is not satisfied in my context. I must start always at position 0 to use this configuration. [/INST] nan n </s> |
<s>[INST] FTview ME and Omron PLC Summary: communicationHello everybody, I have a panel view plus with an Omron plc CJ1M on a ethernet network, but there is no communication. I upgrade the firmware of the panel with the FINS OMRON, but in the communication setup on FT view ME there is nothing. Can someone tell me what to do ?? [/INST] Did this communication work at one time, but no longer works now? If it did work at one time, what changed? yes this communication worked but i changed the communication module of the panel and my computer and i have nothing in the communication setup of RSLink Entreprise in FactoryTalk View application Hello, I was on the site where there is a omron plc CJ1M CPU12-ETN with one panelviewplus 1250 and one panelviewplus 1500. I configured the PFE file in the kepserver folder of the application of each panelview with the last byte of the ip adress in the source node number of the FINS network configuration with the KEPware configuration software version 5.13. Example : Source network adress number :0 Source node number : 2 (ip adress of a panel 192.168.1.2) Destination network adress number : 0 Destination node number : 1 (ip adress of plc 192.168.1.1) Destination unit number : 0 (unit number of plc is 0) I transferred the 8.00-20160418 firware in the two panelview. But there is no communication with the omron plc Someone can tell me where is the problem because i don't what to do Thank you n </s> |
<s>[INST] How to export the current view of a TREND to a REPORT ? or better still PRINT While i like the sound of automated reports , i cant get my head around how you go about sending a preselected TREND chart on a screen , to become a REPORT, that will then become a PDF . the PDF ideally then sent to a known email address. But lets just deal with what it takes to export the Trend ( viewed on a screen live ) and then activate an export function to create either a Print Screen funtion , or create a PDF. I like the PDF feature IF it can capture the view of the Trend, because this leads to a paperless method..well atleast at the control room . The office personal will end up printing out the PDF if required. Table Data is not required at this point , i need the Trend chart printable somehow. Looking out for a video on Youtube RA FT Optix ... [/INST] Hi Stu, I'm not aware that this is possible. If it is, I don't see a way to do it. When you create a report, it comes with method which can be called to generate a PDF of that report. First, though, you must create the report and the format in Optix Studio. The objects you can put on a report are limited. For data, I believe it is currently just limited to a data grid. I don't see a way to put a trend object or to take a snapshot of a live trend chart and put those on a report. You would have to display the trended data in table format by querying the same data store that the trend object is attached to. The ability to generate a trend snapshot or a print screen doesn't exist yet. I'd be willing to bet money it is on the roadmap though. Hi Shane, WOW - well i certainly didnt think this would be the case when i went down the road to invest two weeks of private time and learn this new application from scratch. I only know one person in New Zealand that has even deployed a project to a PC. When i researched RA old school RS view 32 it does it and thats so old , i have made the mistake of assuming the new HMI would do it. It critical that i can print it out . Ministry of Agricuture & Fisheries must be able to view a printout of the product process. For now i do know that i can use WINDOWS LOGO + PRT SCN ..to dump to Pictures/Screen shots ...and it can be then printed from there. However this is long winded and the current old FIX application even prints too with a single click of the button. Well - that PRINT funtion cannot come soon enough else ive wasted a hell of a lot of money using the developer. Without your kind help Id be stumped on a few of these things. Ive learned so much the hard way thats for sure. Don't despair just yet. Just because the tools to do this are not already baked into the Optix Studio IDE doesn't mean it is not possible. Remember that Optix has a .NET backbone, making a lot of things possible. Therefore, you should be able to take a screenshot of the current window using a C# script. Do a quick web search for 'C# capture screenshot' and you will find tons of code from people who have done this already. You would have to create a runtime NetLogic, add directives for using the libraries System.Drawing and System.Drawing.Imaging, and then the code to take the screenshot. This would have to be wrapped up into a method which you can invoke from another object (e.g. a button). You would probably also have to add some file handling code to save the screenshot in the project directory or somewhere else. Optix was a new software product which Rockwell acquired and subsequently pulled under their umbrella to continue development. Not all the features available in the legacy RA visualization products will immediately find their way into Optix, unfortunately. This is one feature, though, that they should look into sooner rather than later. Thanks Shane. I never even realized it wasnt their original product . Im not sure im capable of writing any C .. thats the limit for me. I used to coe basic as a kid 45 years ago. Now i program plc , hmi , run the wiring & ladder , build panels , and install . i dont have anyone to fall back on. I have 10 more years left in me if i dont die from lack of sleep haha. Night , its 2.30 am again . Again, THX. n </s> |
<s>[INST] OPC read of an array Does anyone know how to read an array from CPX using OPC? I have programmed the syncread and can get the first value in the array but how do I get more values? I tried changing the L [/INST] wfk, take a look to the following technote: Aid 8171 Inside there is an example to use OPC in excel , with VBA. I've succesfully modified the file just to add the range of cells to see the value of the elements of the array. The syntax to use to read multiple elements is: [TopicName]ArrayName[Starting Element],Lxx where xx is the number of elements to read. I think you may use this also with VB, removing the excel cell reference and using what you need in your application. I've attached also a screenshot that shows the result. Hope this helps... - fuzzy logic A couple of heads up. Yes the ,LXX should work since in DDE and OPC. But1. The maximum numbers hat you can put in the XX is related to the data type in the array. For Dint & Real types is 121, for Int is 243. Beyond the limits you will get error.2. The array is returned as V1,V2,V3, V4....... so you need to separate the data out in the client.3. As a side note - SyncRead is usually not the best way of doing reads - I would suggest Subscribe and is not then Async. Thanks but this still isn't what I was looking for. The Excel VB code does connect and does read a value but it only reads one item (the one referenced in the subscript of the array [x]) without regards to the value in xx (Lxx). Once the connection is made, how do you parse through the remaining values? For instance, if I connect to array[0],L5 how do I look at the values contained in array[1]...array[4]? In my test I've modified the VBA code of the example to write the value you're reading from array elements to a range of cells... Take a look to the attached screenshot... Hope that helps... - fuzzy logic n </s> |
<s>[INST] Major Fault T01:C61 PLC1: Compacticlogix 5380 Model:5069-L330ER Software: Studio 5000 V32.011 PLC2:Micro850 Software:CCW V12 Yesterday, we got call from our customer that plant was stopped running in Auto mode and PLC(5069-L330ER) shows Major fault T01:C61 Non-recoverable diagnostics saved in PLC display. and Also, OK was Flashing in RED We remotely logged and confirmed the same . When we tried to go ONLINE , a message shows There is no project in the controller for logix designer to upload. Later, we cleared the error and downloaded the backup plant was brought running condition. we are not sure how this happened all of a sudden and how to avoid this future. Looking forward to hear if anyone experienced the same in past and how they resolved this issue. [/INST] That Major Fault could be hardware or firmware related, and there isn't an immediate way to discover the reason that caused the processor to fail. You can find indications about controller behavior and fault troubleshooting inside the following technote: QA10691 Looking at the firmware version you're using inside your Logix controller, I remembered of a known issue which can cause a MNRF (Major Non-Recoverable Fault) which has been resolved with firmware 32.012 Here an excerpt from the Release Notes: A Background Diagnostic Can Cause the Controller to MNRF (00222116) Corrected Anomaly in these controllers: CompactLogix™ 5380 Controllers Firmware Revision 32.012 Compact GuardLogix® 5380 Controllers Firmware Revision 32.012 CompactLogix 5380 Controllers Firmware Revision 30.011 Known Anomaly in these controllers: CompactLogix 5380 Controllers Firmware Revision 32.011 Compact GuardLogix 5380 Controllers Firmware Revision 32.011 CompactLogix 5380 Controllers Firmware Revision 29.011 The controller can experience a major non-recoverable fault (MNRF) due to a background diagnostic that is not properly configured (the diagnostic is not user configurable). I strongly suggest to upgrade the CompactLogix 5380 firmware to a version 32.012 or newer. Hope this helps, fuzzy logic Please don't forget to use the LIKE button and highlight the decisive answer : REPLY > Make Best Answer n </s> |
<s>[INST] SLC500 Hi, have a problem with my SLC500 (5/05), every time i power it on, it goes to fault,When i try to go online, tells me, cannot go online with faulted processor (0002h), so i have to download again and go online, then works fine I found this code in the Help0002 Unexpected hardware watchdog timeout. This non-user error occurs at power up. but i dont know how to fix it.need help,thanks [/INST] Here what is suggested by enginners: If the error code persists replace the processor and/or any other associated hardware (chassis, P/S and any IO modules installed in the system). Also see Technote 15763 (Checklist For SLC-5/03, 5/04 and 5/05 Install Issues That May Result as Memory Clear or CPU Errors) for further items to check in order to clear this error. (Be aware this is a TechConnect users reserved document) - fuzzy logic Although Fuzzy's answer probably isn't the specific answer we'd like to read, I can speak from experience that it's the way to go. Let me suggest an individual order of replacement: processor, power supply, rack, lastly I/O modules. This is not to say that an I/O module cannot cause the issue but from what I have experienced with that same fault over the years, this is the order in which I would replace the parts - all other factors being equal. If the rack is 15 years old, used in a corrosive environment and everything else is fairly new, then I'd look at the rack first of course. n </s> |
<s>[INST] Micrologix Comm through USB port. Is there a USB cable for communications with a Micrologix? If so, what is the part number? Thanks. [/INST] Rockwell has an item that is used to convert an USB port to an RS-232, to be used with DF1 protocol. Item is 9300-USBS. Normally you may use a 1761-CBL-PM02 cable with it. Hope this helps... - fuzzy logic Will any USB to serial adapter work or does it have to be the 9300-USBS? Dale It can be any usb to serial adapter but sometimes cheap adapters do not work or communication breaks often. You may try any industrial usb to serial adapter. Thanks. I found an adapter made by TRIPP-LITE, model USA-19HS that works perfectly. Dale n </s> |
<s>[INST] Best type of device to activate registration input 755 drive Hello, Looking for some advice/thoughts around an eye that I can use to detect the front edge and back edge of an Oriented Strand Board mat moving around 2700 mm/sec. We are getting false detects and I am looking for something that is more accurate. We currently are using 42BT-B2LBSL eyes. [/INST] The sensor you've indicated is a background suppression sensor. What's in the background behind the OSB mat? If your OSB is running on a flat belt or mattop conveyor, you're probably not going to any more successful than you already are. If your OSB mat runs on a roller conveyor, make sure there is nothing below the rollers for a significant distance, and make sure the sensor is centered between the gaps of two rollers. Make sure the gap between rollers is significant as well. Ideally, a through-beam or retroreflective sensor is far better in position-sensitive registration applications such as yours. n </s> |
<s>[INST] DriveExecutive program Summary: DriveExecutive backup file not openingDear All drive executive installed on my computer but what could be the reason why the imported driver doesnt open backup files blank page open , does not give error I checked on another computer the versions are correct my computer only opens the backup file it received what would be the reason Thanks [/INST] My computer only opens the backup file it received Could you explain this in a different way? Do you mean your computer will only open .DNO files that it creates and will not open .DNO files created on a different computer? Rockwell doesn't really support DriveExecutive anymore. Rockwell is pushing everyone to use CCW. You might try opening the DNO file in CCW. In addition, DriveExecutive does not work with 520 and 755T drives. You have to use CCW with them. Could that be your problem? yes right it just opens the backup my computer took .dno files backup driver powerflex755 Do this. Start DriveExecutive using the start menu. Do not double-click on the .DNO file. Once DriveExecutive is open, use the file menu to open the .DNO file. We've seen that behavior but it is inconsistent. I'm guessing you're running Windows 10? We saw this behavior when we started using Win10 computers. It's inconsistent, sometimes double-clicking on a .DNO works, sometimes not, even on the same computer. I usually have no problems, but my boss with the same computer cannot double-click on .DNOs to open them. He has to only open them only after DriveExecutive is already open. yes, one of the two computers works as you said and the other one does not work at all. I am having problems with win10 You can try uninstalling / reinstalling DriveExecutive. If that doesn't fix the problem, you could try contacting Rockwell Tech support. The other option is to use CCW to work on your 755 drives. I'll try thanks n </s> |
<s>[INST] is it possible to export, edit the .CSV and then import the new tags? Hello, is it possible to export, edit the .CSV and then import the new tags? I can export, then I edit the .CSV adding some tags, then the import error occurs. [/INST] Yes! I've done it a thousand times :-) But you must insure the format doesn't change. Compare the old file to the new and you'll probaby find something missing in the new. To avoid that, I always create a test tag of each type, and then in Excel I duplicate those. Also be careful with Excel when you save your CSV. PS - If you are still having issues share your FTView version and Excel version, and before and after files to if that's cool ;-) Shawn Yes, I agree with Shawn and the suggested test. I've prepared a procedure for another user here in the Community, please follow this LINK Just follow the indicated steps, not considering the Alarms part because doesn't apply to you; you should have only one file exported (Tags) and the same file once modified to import in FactoryTalk View SE. You'll see the procedure mentions the Export, the edits in Excel, how to save the modified .csv file (this is the most important part) and then the Import back. This is a working procedure I tested many times and with different software versions. Hope this helps. fuzzy logic Please don't forget to LIKE and highlight the decisive answer: REPLY > Make Best Answer Hello, thanks for the help, it really was something different in my excel (.CSV) when editing, I saw a comment on the internet saying to edit in a notepad, so I did it and it worked. I believe that Excel uses different line termination characters by default. If you try to use Save As, then you will find at least 4 different CSV formats offered with one additional format under the Export. You may need to experiment with them and maybe open CSV file in a Hex editor to see byte-by-byte difference Excel is notorious for modifying a CSV from the form expected by FactoryTalk applications. I use Visual Studio Code (free) for that reason and haven't looked back. You can do regular expressions, mass find and replace, and the existing format will remain unchanged. I even use it for Studio 5000 AOI/UDT work and it's awesome. n </s> |
<s>[INST] 865 Medium Voltage Differential Feeder Protection Summary: 865 Medium Voltage Differential Feeder ProtectionHi What is the exact part number for 865 Medium Voltage Motor & Feeder Differential Protection? http://ab.rockwellautomation.com/Circuit-and-Load-Protection/Medium-Voltage/865-Medium-Voltage-Protection [/INST] check page 45 of this document http://literature.rockwellautomation.com/idc/groups/literature/documents/br/1503-br010_-en-p.pdf n </s> |
<s>[INST] VPC Control With Powerflex 755 Summary: Can a Powerflex 755 control a VPC servo motor in an electronic gear configuration?I'm looking for a solution to synchronize a servo motor to a master encoder. The servo motor is fairly large (22kW) and an MPL motor did not match all the needed specifications. I know a 5700 drive is ideal for a VPC servo, but this needs to be a standalone configuration. In the past I've done this with an AC motor and two encoder cards in the Powerflex 755. Is there any reason why I should not do this with a Poweflex 755? [/INST] nan n </s> |
<s>[INST] Commands that not run on HMI Server Hi! ther are some commands that not run on HMI Server, but in standalone app this is a problem. Example: I need a PopUp display to appear when tag value is equal to 123 configuring an event can't do it because display command does not run on HMI Server, so I need deal whit VB code and a numeric display which visible properties are set to false. This is a little problem if you need this on 1 display, but what happen if need it on 20 displays? we need put this numeric display on 20 Displays!! This is a solution for this case Now I need execute the command SupressOff SomeTagName when tag value's is equal to 12, I have 23 Tags that need execute this command on 20 displays... this is hard to maintenance Some one known who to launch events in some way that run like in command line?? [/INST] Hi Psycrow, The events in SE run at the server, not at the client. So if all you do is execute a Display command, there is no way to tell it to run on a specific client computer. So what you need is a way to get the client to issue the Display command. Tech note 22007 talks about a way to do this using VBA. In your case, you want to add a numeric display on a graphic that is always running, perhaps not visible. The object looks at your tag and when the value changes, you test to see if it is equal to 123. If so, you execute the command Display SomeScreen. Same principle for your SupressOff command. In addition, remember that the client MUST be a Read/Write client to execute any commands. Actually, it depends on what the command does. For example, a Display command can be issued by a Read-Only client. An Set command, = command or Acknowledge command cannot. I think the Acknowledge does not work because an alam acknowledge writes to the alarm ack tag, alarm handshake tag, etc. n </s> |
<s>[INST] FTASecurity Service shutting down As part of my DataView install, I have had to install the security provider FTASecurity. I see that this is a windows service. However after running the instal .bat, everytime I start the service it shutsdown without an error. The help message is: HELPMSG 3534 Can anyone please help? Thanks [/INST] Gary, On my machine, FTAServices is configured to run as a Local Service. Phillip, Thank you the post however it is FTASecurity service and not the FTAServices service that I am having issues with. Gary Muir, as I can see you're trying to get info about FactoryTalk Analytics Security Provider. You can start from the following technote: QA57745 - FactoryTalk Analytics Platform Frequently Asked Questions (FAQ). The technote refers you to the Security Provider Advanced Installation Guide, which is available in the documentation folder: However, I strongly suggest to contact Technical Support for this problem, to be better assisted. fuzzy logic Please don't forget to LIKE and highlight the decisive answer: REPLY > Make Best Answer n </s> |
<s>[INST] Program Mode not working Dears, I have two 1756-L73K controllers in a redundant configuration. A couple of days ago, the Program Mode, which was working fine, had its icon changed to blue color and is not working anymore. I still can make online changes in Run Mode, but the Program Mode is no longer available. I downloaded an old program, to see if it was a logical issue, but did not work. Right now I am commissioning the system and appreciate your help. Thank you very much, Coiti [/INST] This means your physical PLC key is in Remote and you have it set to program mode. Click the blue icon dropdown button and switch to Run. Juan. Dear Juan, thanks for your reply. Yes, the PLC key is in the Remote position (I have already tried to switch from REM to PROG to RUN, a few times), and yes clicking on the blue icon I can switch the PLC to Remote Run. But before this issue, the Remote Program was in green color and I could edit the program online. In Remote Run, I can also make online changes, but why Remote Program is not available anymore? If I leave the PLC in Remote Program (with the blue icon) the program actually is not running. I don´t think the blue icon is a normal icon. Thank you very much, Coiti I think you were mistaken when you wrote Remote Program was in green color. Remote Program mode is blue. The processor is NOT running the program. You can make changes to the program and and they are immediately accepted into the program code. Remote Run mode is green. The processor is running the program. You will see the current program and the new edits both in the program, with the D, I or e symbol instead of the rung border. You have to then Test and Accept the edits to get the new changes to replace the old code. As Juan said, click the Rem Prog or Rem Run icon symbol to change between modes. Best wishes, Ian If I understand correctly controller does not transition from Run Mode to Program Mode or it takes a long time to transition. Here is one Knowledgebase ID that explains what might be possible going on. https://rockwellautomation.custhelp.com/app/answers/answer_view/a_id/7448 Do you get the message that controller acknowledged the transition request? Does it transition properly from Program Mode to Run Mode? n </s> |
<s>[INST] FactoryTalk Transaction Manager As i am new to Factory talk transaction manager.I am using the Factory talk transaction manager for logging the RS View 32 data to SQL server 2005.I have configured it and able to log the data in SQL server columns but my issue is i have to log the array of tags(60) into one praticular coulumn in SQL server database.So how can configure the transactions in Transaction Manager or any other way of getting out of this problem.Thanks. [/INST] You have to make 60 transactions. For distinction of each variables you can add aditional column with tag id. My customer had the same problem and it was reason why they don't use Transaction Manager, but freeTuxEIP and Linux. What you can do is create a Stored procedure that takes 60 parameters in a FTTM transaction and then manipulates them into 1 column before inserting it into the DB. The key is that you need to create the SP in SQL server and not it FTTM, and then map the SP as a data object. The power of FTTM comes from creating SP's in SQL server and then mapping parameters to it. To create a SP, Google how to create SP's with parameters and how to manipulate data. n </s> |
<s>[INST] Software Versions If I have multiple firmware versions loaded into my PC from one diskette, can I toggle say between version 13 and 15? Thanks in advance for any help provided [/INST] Not sure to have correctly understood your needs.... anyway, you can open multiple instances of the RSLogix 5000 on one PC using different software versions, and freely switch between them... There could be some possible issues with this, see Aid 39470. If it is not your request, please post again and give more details...:smileywink: Hope this helps… - fuzzy logic Yes, I am trying to figure out how to switch between the different versions...10.1,13.1,15.2...etc Thanks again! Ok christina, so has this solved your request ? If so, then may you please close the thread using the green Solution button over my previous post? Thanks,- fuzzy logic n </s> |
<s>[INST] RsLogix Emulate 5000 Dear All, I want know how to work in the RsLogix 5000 Emulater tool.If anybody having the user guide for this means please let me know or send to my email id(sampath.j@metsys.co.in) [/INST] You can find from the link below http://literature.rockwellautomation.com/idc/groups/literature/documents/gr/lgem5k-gr015_-en-p.pdf It works like ControlLogix 5000. But you have to use 1789-SIM module for I/O in RSLogix Emulate 5000. When you are programming an emulator CPU in RSLogix 5000, you will locate 1756-MODULE for I/O in I/O Configuration tree. n </s> |
<s>[INST] CCW Powerflex Instruction Good afternoon, I am using a Micro850 Controller with a PowerFlex 525 VFD. In my programming in CCW im using the RA_PFx_ENET_STS_CMD Function Block to communicate with the VFD over EthernetIP. My question for you guys is, this function block has an Input labeled EnetCntrlTO_sec What is that used for? Thanks, Eugene [/INST] Based on nomenclature alone I would hazard a guess that is a communication timeout value. EDIT: Found a technote: QA57091 Table from the technote: Regards, RM Ahh I see that now, dang that didnt occur to me. Thanks Ryan for pointing that out. n </s> |
<s>[INST] SFC - Last Scan of Active Steps Hi, I have problem to understand tab 'SFC Execution -> Last Scan of Active Steps'. There is three options: - Automatic reset - Programmatic reset - Don't scan. When i found information about this is short information not explaining what is this. Can anybody help me to explanation what is a difference between? [/INST] Welcome to Engage, Jan! I suggest to review the following manual, starting from page 35: https://literature.rockwellautomation.com/idc/groups/literature/documents/pm/1756-pm006_-en-p.pdf Options are explained there; if you still have questions after reading, please post again. fuzzy logic Please don't forget to LIKE and highlight the decisive answer: REPLY > Make Best Answer Hi, thanks for the help fuzzy logic. Is stupid but i read what you send to me and now... i understand. Maybe i focus to much for problem not for solution. Thanks again! n </s> |
<s>[INST] FTV 13 Test Application fails to recognize tags Hardware: PanelView Plus 7 Performance, ControlLogix 5580 Controller ver 34 firmware Software: FTV ME ver 13, Studio 5000 ver 34, all firmware latest on ControlLogix modules After upgrading to ver 13 FTV, and Studio 5000 v 34 running the FTV 'Test Application' feature results in all tags failing to be recognized by the processor. The PanelView programs run fine on the physical hardware, but Test Application is useless now. I called tech support and they told me it was incompatibility with Factory Talk Linx 6.30. This was about a month ago and 'Test Application' still fails to recognize legitimate tags. Any info on this issue? [/INST] Welcome to Engage, Tye! I'm moving this thread to Automation Control, where it is better suited. If you are not already a member of the Automation Control community and want to continue this conversation, you will be prompted to join that community. My suggestion here is to apply latest patch rollup from the following technote: QA49264 After that one, please apply also the newest patch from the following technote: BF27932 This last one is related to a known communication issue identified in the last release of FactoryTalk Linx, as explained HERE. Thank you, fuzzy logic Please don't forget to LIKE and highlight the decisive answer: REPLY > Make Best Answer Thank you! The BF27932 patch worked. Note: When I called TechConnect about a month ago they did not seem to be aware of this patch. Good to know, I'm happy for that! The patch has been released on May 2, there are chances it was not yet available when you contacted them. fuzzy logic Please don't forget to LIKE and highlight the decisive answer: REPLY > Make Best Answer n </s> |
<s>[INST] Problem in writing RSView32 project to CD ROM Hi, I`ve burned the RS View 32 project in to a CD. The memories of both the source and destination are same...... But... when i try to open the project from the CD in the same system, i `m getting the error message as attached [/INST] The application was saved on a CD. Copy the application folder directly on your hard drive. Reference Aid 48060 - fuzzy logic n </s> |
<s>[INST] Rslogix 5000 std & 9324-RLDMLPE Summary: Rslogix still reporting editors are not installed Hi, I have been using Rslogix5000 standard edition versions 10, 11, 13, 16 & 17 utilising just ladder, however I now need SFC and function chart so bought 9324-RLDMLPE multilanguage pack and have downloaded the concurrent activation, but I am still unable to access or create function chart files. Rslogix is reporting that the required editors are not installed. Can someone please let me know where I'm going wrong (pretty please) Steve [/INST] Welcome to the Forum ! Chances are that your license hasn't been properly activated... did you check inside FactoryTalk Activation Manager ? Which is the HostID selected ? Inside RSLogix5000, open Help -> About --> More Info button you may find the installed (activated) Components for your software. - fuzzy logic In order to enhance the reputation of the Forum's contributors, please rate the replies you got and remember to close the thread clicking Choose as Best Answer button over the solving answer. Thanks ! I also have just purchased 9324-RLDFBDENE to enable FBD on existing version of RSLogix5000. Off I went to the download centre and selected my product to download (link from the order email), but a wee file of 118 bytes downloaded - just a text file called NoMedia.txt containing the words This catalog is an activation only catalog, and does not include software media or allow software to be downloaded. So how do I add this functionality to an existing RSLogix5000 install and how do I activate it? Hi I am unable to get software backup of RSlogix5000, do any one can help me out? I failed to download it from Rockaoutomation web site too. Regards, Mansoor Fuzzy_logic is correct, the language add-on licences don't require the download or installation of additional software, the presence of the activation on the host computer should be enough to unlock the additional language features already present in your installation. If the editors are not available, double-check your activation for the MLP is valid and listed as available. n </s> |
<s>[INST] Rockwell Powerflex 700 faults auto reset EDIT: Removed links to external community probably added by the user via copy/paste of the thread -FL Have 700's and 753 VFD, in the 753 parameter P348 [Auto Rstrt Tries] can't find the parameter for the 700 to activate this feature. TIA.. [/INST] Welcome to Engage, Frank! See the following manual, page 41: https://literature.rockwellautomation.com/idc/groups/literature/documents/um/20b-um002_-en-p.pdf Param. 174 in PF700 drives is Auto Rstrt Tries: Hope this helps, fuzzy logic Please don't forget to LIKE and highlight the decisive answer: REPLY > Make Best Answer n </s> |
<s>[INST] How to assign HMI tags/constant value for Display Element - Process Library v4.0 on FactorytTalk View ? Good morning everybody. How we can assign HMI tags/constant value for Display Element - Process Library v4.0 ? I mean for example assign value 5 for parameter [/INST] Phong, the procedure for using Global Objects is described in the page you posted: The value can be a tag, backing tag, or numeric or string constant. You can find the procedure described in the Reference Manual as well, starting from page 40: Rockwell Automation Library of Process Objects: Display Elements, publication PROCES-RM014 fuzzy logic Please don't forget to LIKE and highlight the decisive answer: REPLY > Make Best Answer Thank you. n </s> |
<s>[INST] Control Net Setup Hi, i need a step by step guide on how to setup a ControlNet network with remote Flex IO. I also need to know how the network addressing of controlnet works and how to set that up. Have already connected the ControlNet CN2 module as the local module and the remote module is the ACN15 CNET adaptor with Flex IO connected to it.Have already created a project and created the Network tree in the project. Just need to make the network work now. Thanks. [/INST] Although you're already at an advanced step of the setup of the network, I suggest first to review the Controlnet for Logix User Manual, there are many useful infos you're searching for. It will also be important to avoid common errors in the setup. There are also many technotes that could help you, all of them require a TechConnect authorization. Here following some of them:Aid 46577 - Aid 28464 - Aid 18056 Then, if you still have doubts, you will be able to be more specific on a new post... :smileywink: Hope this helps… - fuzzy logic Thank you, will shout if i get stuck...I am sure that will be very soon... Hi, how do you set the ControlNet addresses, is there some form of dial to set them on the device, or is it just the node address assigned within the RSLogix project or do you setup both? For both -CN2 and -ACN15 there are network address switches to set on the module. Obviously you've to use the same node address selected by hardware, when configuring the module inside the software. - fuzzy logic n </s> |
<s>[INST] update the total in a totalizer block Summary: Can you update the total in a totalizer block to compensate for offline programming time?Can you update the total in a totalizer block to compensate for offline programming time? [/INST] Yes you can, I did it using ST for both current and old total //Object: Place an operator specified value into running totalizer fields //mac 9-18-2014 //---------RESET THIS RUN VOLUME Thanks, Splash. We took your code, made it ladder for this application, and used it over 50 times. Much appreciated. n </s> |
<s>[INST] FTView 5.1 and Server 2008 Issue - IIS 405 Error I can't get passed the The server... is out of service error when attempting to save a display hosted on a Server 2008 machine from a client running XP. In the IIS logs on the server 2008 machine I get: 2010-02-09 14:20:19 192.168.100.10 PUT /rsviewse/HMI_Server/gfx/alarm_summary_new_fcb19a30-2fed-4eb3-a8aa-8d1100149c43.gfx - 80 - 192.168.100.20 View+Studio 405 0 0 23 Display opens and saves ok from the server, just not on any networked FTView Studio machine. Any ideas? [/INST] Please take a look to the following technotes: Aid 30232 - Aid 40564 Double check also the correct installation of IIS... HERE the correct procedures.... Hope this helps… - fuzzy logic Thanks for the reply. Aid 40564 describes my problem exactly. However, I checked the folder security permission settings and they look ok. Double checked my IIS install, that looks ok too. Tried deleting the temporary internet files... no luck. n </s> |
<s>[INST] error code 21h Summary: error code 21hI have an error code 21h on a 1747 L542 series C processor. I suspected an output card. I removed all of the IO and loaded a blank program into to CPU. I was going to introduce the IO back to the rack one at a time to see which card was causing the issue. The CPU faulted immediately after I went to Run Mode although I had not yet returned any IO to the rack. I am thinking I may have a bad rack. Can anyone confirm my suspicions. [/INST] If the error code you see is 21H it is actually error 0021H. In SLC 500, the first two digits rep[resent the salot number of the module from wehre the fault originated (in this case '00'). So it's a fault in side the controller but not necessarily the result of an output card. The second two dgits are the actual fault (21H in this case). There error is in the controller. RSLogix 500 Help screens list the major fault codes. Seek out Major Fault xx21. Thanks for the reply. After loading a blank program with no IO inserted in the rack, the controller still immediately faulted. I installed a new rack and the controller has been running just fine for about a week. Thanks for the reply. n </s> |
<s>[INST] L63S Processor not recognized in Factor Talk View ME I'm trying to setup communications to my 1756-L63S Processor (maj. Rev 17) and it is not an option in the factory talk view. The safety partner is there (L63SP), but no L63S. I'm running FTVME Ver.5 CPR 9 with the latest patch installed, and RSLINX Classic Lite Rev. 2.54.00.11 CPR 9 SR 1. Any ideas??? [/INST] That processor is available for selection in latest FactoryTalk View revision 5.1... (RSLinx Enterprise 5.20) May you consider the possibility to upgrade your current software version ? - fuzzy logic I thought I had the latest version. I just got it 3 days ago from rockwell... I'll update the software when I get back to work on Tuesday. Thanks for the heads up.... n </s> |
<s>[INST] Do I need to replace all the remote ControlNet module during upgrade Redundancy Controllogix? such... Summary: Do I need to replace all the remote ControlNet module during upgrade Redundancy Controllogix? such as the remote module 1756-CNBR/D located in remote chassis.Dear, When I upgrade the Redundancy system from CLX-L55M12 v11.16 to CLX L71 v20.055, I should replace the CLX-L55M12 CPU with CLX-L71 CPU. I should replace the 1756-CNBR/D module with 1756-CN2B also. (Because of the 1756-CNBR not compatibility with CLX-L71 redundancy) Do I need to replace all the remote ControlNet module during upgrade Redundancy Controllogix? such as the remote module 1756-CNBR/D located in remote chassis. Do I need to upgrade the firmware for all the remote Adapter 1794-ACNR15? The original Redundancy configuration ====Redundancy Chassis================= 1756-PA72 1756-A4 [0] 1756-L55M12; V11.16 ? [1] 1756-CNBR/D; V5.16 ? [2] 1757-SRM; V3.25 ? [3] Fibre Cable 1756-RMC1; Length 1 meter? 1756-PA72 1756-A4 [0] 1756-L55M12; V11.16 ? [1] 1756-CNBR/D; V5.16 ? [2] 1757-SRM; V3.25 ? [3] ====Redundancy Chassis================= .... Control Net .... Control Net .... .. .. ====Remote Chassis 1================= 1756-PA72 1756-A4 [0] 1756-CNBR/D; V5.16 ? [1] 1756-ENBT/A; V1.1 ? [2] 1756-ENBT/A; V1.1 ? ====Remote Chassis 1================= .... Control Net .... Control Net .... .. .. ====Remote IO station 1================= 1794-ACNR15/C 1794- 1794- 1794- 1794- ====Remote Chassis 1================= (There are total 9 Remote IO stations) .... Control Net .... Control Net .... .. .. ====Remote IO station 9================= 1794-ACNR15/C 1794- 1794- 1794- 1794- ====Remote Chassis 9================= [/INST] 481872 - 1756-CNBR/D in the I/O chassis when using v19 ControlLogix Redundancy system? Access Level: TechConnect Date Created: 04/16/2012 10:09 AM Last Updated: 01/14/2015 03:27 PM Question I want to migrate to the newer Enhanced redundancy using L7x, CN2 and EN2. However, the I/O chassis are on ControlNet and have CNBR series D. Can these be retained or is there any need to replace with the series E of CNBR? Answer Yes , the Remote I/O chassis can use a 1756-CNBR series D its only the Redundancy chassis that has to follow the correct series and firmware revision n </s> |
<s>[INST] PID 4-20 to 2x output Hi All, Can anyone enlighten me please. We have 2 types of actuators that need to be controlled from Contrologix. One type of valve has a typical 4-20ma and this is stratight forawrd to implement. We also have some SDK32 actuators that are mains controlled with 2 wires, one wire drives the actuator to close position and the other one to open. I would normaly use Omrons to control these but this is not an option in this aplication and controls need to be in PLC. Any ideas? Thasnk a lot! [/INST] Hi Jay Kay, I hope you mean Siemens SKD32 Electro-hydraulic actuators? The 2 Signals to open or close are 230V AC so you will either need a Relay Card (Like 1756-OX8I if you are using 1756 Racks) or any 24V DC Digital Output Card (Like 1756-OB32) to drive a Relay that can switch 230V AC. Is your question already answered or do you need to know how to control these digital outputs with a PID? I'm not really sure what your question was aiming for. Please get in touch if you have any further questions. If this answer helped you, please Like. If this answer is the best please REPLY-> Make Best Answer Hi GRO, Sorry I will try to clarify. At the minute I use PID instruction to calculate a 4-20ma signal that sends the old actuator to the required position. 4ma fully closed, 20ma fully opened. That's straigh forward. We are having few SKD32 Siemens actuators and thay do not take 4-20ma to set the stem position. What I am trying to establish is how would a simple code look like to mimic PID controls so I can have PV on a setpoint. Normally I would use and Omron controller and happy days. I cannot use them in this application though. Jay Kay, You could try using the Position Proportional instruction (POSP) in Logix. The output (CV) of the PIDE instruction would be connected to the SP of the POSP instruction. Normally, you would have a Position feedback from the valve to know the actual actuator position. In the case of the SKD32 valve, it looks like it does not have a feedback. In this case, you could use the previous value of the PIDE output as the Position feedback on the POSP instruction. Therefore, if the PIDE output is increasing, the OpenOut of the POSP instruction will pulse to open the valve. If the PIDE output is decreasing, the CloseOut of the POSP instruction will pulse to close the valve. Regards, #LogixDesigner Hi Keith, Does it look like something you were thinking about? Previous PIDE output - I just sample CV every second and use it as position feedback. Put the PIDE in a 1 second task Put the POSP in a 50ms task. Connect PIDE.CV to POSP.SP Connect POSP.OpenOut and POSP.CloseOut to your valve Open/Close relays In POSP, set OpenRate, CloseRate, and CycleTime. If your valve requires 10 seconds to open and 10 seconds to close, Then OpenRate = 100% per 10 seconds CloseRate = 100% per 10 seconds CycleTime = 10 seconds When the PIDE wants to move the valve from 50% to 55%, which is a 5% change... the motor must run for 5% of 10 seconds which is 500ms. Because the POSP is in the 50ms task, the POSP will hold the OpenOut high for 10 x 50ms = 500ms Another option would be to use the P_ValveC add-on instruction from the Library of Process Objects (4.10) for PlantPAx. This instruction can be configured to simulate feedback for a valve that doesn't provide any (or only provides limit switches for fully closed or fully open). You need to set up the configuration parameters for the rate at which the valve opens (% travel per second), the rate at w hich the valve closes, and the deadtime (time between triggering an output pulse and the valve actually moving when changing direction). If the simulation drifts away from the actual position and the valve has limit switches, the instruction will reset the simulated feedback to zero when hitting the closed limit, or to 100% when hitting the open limit. See publication PROCES-RM013 (search on Literature Library) for more details. Dale Hi Jay Kay, To quote Doris Day from the movie Annie get your Gun: Anything you can do I can do better If you normally use Omron then how do you do it with Omron?! If you already have an algorithm then surely you can re-implement the Omron code in AB - I'd be surprised if anything Omron can do, AB can't do better....(excuse the flag waving) If you're lacking the algorithmic approach for either platform (like I suspect) then from my cursory analysis - without position feedback from the hydraulic actuator you're pushing the proverbial up hill. The CV output of your PID is conceptually an absolute term expressing how much actuation the system should be applying, however your extend/retract digital control lines of the actuator only offer RELATIVE MOTION control of the actuator - and marrying the two is notoriously difficult. Now, you might think that say Homing the actuator against (say) a proximity sensor and then trying to keep track of it's position through some calculation (rather than some actual position sensing) could work but in my experience this is very difficult because errors will inevitably accumulate and sooner or later the calculated values bare no resemblance to reality - things soon stop working. I suggest you look for a position feedback device to apply to the actuator (or some other part of the machine for an indirect measurement) so that Keith Hogan's neat suggestion can be applied Perhaps look at the position sensing Swiss-Army-Knife: the Draw string encoder or Laser Distance measurement sensors if the more common methods cannot be applied. Cheers Patrick Hi Patrick, Saying OMRON I meant E5EC temp controllers. I fully agree that this exercise seems to be pointless as there are too many variables. Hi Jay Kay, At the risk of making a liar or fool of myself.....if temp control is what you require then maybe an approach like this may work: *NOTE: This is probably a Hail Mary suggestion! All standard disclaimers apply. In code have your PID loop's Setpoint permanently fixed at 50% - this never changes. Separately, you have a variable(tag) that holds the desired SP temperature (in Eng Units) for the System You can still control the temperature the PID loop tries to achieves by dynamically (re)scaling your incoming PV (which should be in Eng Units) such that the desired temperature is reported to the PID as 50% That is : If PV% is the scale process variable we pass to the PID then : PV% = PV/ 2* SP Now, just as the (50%) SP set in the PID is artificial, the CV coming out becomes 'artificial' in that it will always tend to settle around 50% regardless of desired temperature ....this is because we implement the following actuator control logic: IF CV > (50% + dead band*) THEN Drive actuator Fwd** IF CV < (50% - dead band*) THEN Drive actuator Rev** ELSE do nothing * salt to the application's taste **swap the directions for opposite action This logic should drive the actuator to the right physical position (without needing to know the actuator's position) based on the amount of time the CV spends above and below 50%. In other words, it should work because we have manipulated the meaning of CV - we can now interpret it to mean whether the PID loop needs the actuator more open or closed, or to be left where it is. It is essential to add code that when the loop is not running (manual mode) the CV is forced to 50% - this is where we want the loop to start from when it enters Auto so that there is no motion initially and if necessary motion can start in either direction as reqd. Tuning of the loop shouldn't be too affected. Recommend you do some code simulation and get a sense of whether such an approach would work for you. Either way, Good Luck! Cheers Patrick n </s> |
<s>[INST] Data read between 1768-L43 and 1769-L33ER PLC. Hello! I am trying to read data from a 1768-L43 PLC which has a 1768-ENBT card and a 1794-AENTR module which has all the variables I need (Picture 1), into a 1769-L33ER PLC which is in an other project. The 1794-AENTR module has an IP address of 192.168.1.11, my problem is that in the other project which has the 1769-L33ER PLC in it already has a device with the IP address of 192.168.1.11 (Picture 2). I tried adding the 1794-AENTR as a new module into the other project but it of course showed an error of duplicate IP addresses. How could I reference the path to the 1794-AENTR module for messaging? [/INST] You can't connect the L43's local network to the L33's local network if there are duplicate addresses. The options I see are: Eliminate the address conflict Connect your L33 to the L43's other Ethernet module via a NAT device. Are these networks even physically connected together? It seems to me these are both private IO networks and are segregated from each other, hence the duplicate IP addresses. What's the IP address of the ENBT in slot 2,named VLAN681? That looks like it may be your plant network. You'll probably need to connect the L33 to this network using a NAT device of some kind, since I don't believe it can have more than one IP address. The ENBT named VLAN681 has the IP address 10.231.154.80. Can I read data from the I/O modules in Picture 1 from ENBT named VLAN681? If that was the case, should I add that as a new device to the other program and give it the IP address 10.231.154.80? Or should I just set up a message and give the Path : 10.231.154.80,1,2? I think you can only access the I/O in listen only through the network, not the L43's backplane. I think the easiest solution is to NAT the L33 onto the 10.231.154.xxx network and MSG the AENTR's I/O tag from the L43. I don't know how your plant it networked, but from what I'm seeing I don't believe these networks are physically connected. As JJ mentioned, you'll need to install a NAT device (Rockwell makes the 1783-NATR, or there are other solutions) and run Ethernet cable between these two controllers. You'd then need to configure the NAT to translate your L33 from its private IP address, 192.168.1.xxx, to an unused address on the 10.231.154.xxx subnet. Thank you for the answers! Once I'm done connecting these two devices with the NAT device, i have to add both devices to eachother's projects, or can I just set up a message in the L33 and use the path 10.231.154.80 to read the variables i need? (They're all analog INT values.) Also, how should I approach using only one MSG to read the variables marked in the picture below instead of 6 separate MSGs? I guess my question is how do I move these 6 INT variables into a STRUCT, or STRING and make it possible to be read in one MSG? If you're only reading from the L43, you would only need to put the L43 in the L33's I/O configuration. It's not necessary for a MSG instruction, but it can be easier in a lot of cases versus figuring out the path manually. As for your 6 INTs, I think the easiest way is to add code to the L43 (six MOVs) to copy the values into an array and do a CIP Data Table Read MSG in the L33. To tag onto this answer, having the other PLC in the IO tree can make it very easy to generate the message path. Once your message is working, you can then delete it from the IO tree, your message path will still be intact. I prefer to remove PLCs from the IO tree, since they actually burn up an Ethernet/IP connection, which are limited in the CompactLogix world. Thank you. I created an INT[6] gave it the name VAR_MSG, and wrote a code to move my 6 INTs into VAR_MSG[0], VAR_MSG[1) ...etc. In the other project I created another INT[6] called MSG_VAR for my destination element. When I choose a source, and destination element for the MSG I only need to pick VAR_MSG and MSG_VAR and set the number of elements to 6? (Picture below) What it reads from VAR_MSG[0] gets saved in MSG_VAR[0] and so on? Yes. Either VAR_MSG -> msg_var or VAR_MSG[0] -> msg_var[0] will work. If you don't specify the element number, it will imply that zero is the first element. n </s> |
<s>[INST] rslogix 5000 conversion Is there any conversion tool for converting rs5000.acd programs back to rs500.rss programs?Thanks in advance for any input. [/INST] Unfortunately no, there isn't. :smileysad: - fuzzy logic n </s> |
<s>[INST] PowerFlex 700 Frame 5: Replacement of Heatsink Fan Hello, What is the difference between Part No. SK-G9-FAN1-F5 and SK-G9-FAN2-F5 Thanks [/INST] The FAN2 is the new repacement for the FAN1 Hello David9 Thanks for your reply. I have one of the old version on stock. Can i use them without hesitation or are there any improvements? THe fans would be the same size, not sure on the change, but I would check the fan transformer tap position as wellIf the 400v tap is used on 415v supply the transformer or fan can fail, also see Tech Answer note 36968 I have made a short aggregation of findings: - SK-G9-FAN2-F5 is the replacement of SK-G9-FAN1-F5.- The new Type is built with a metal blade fan in place of plastic blades.- If you have any problems with F8 heatsink overtemp, you should check the fan and the transformer- In case of transformer failure have a look at knowledgebase tech note 36968. Thanks also for support by David9 EnjoyJörg Peter n </s> |
<s>[INST] PowerFlex Not Enabled- STS is flushing Yellow Hi all, I have problems with PoweFlex. STS LED is flashing yellow and as I can see from the display the driver is Not Enabled. I have checked in User manual it say if Flashing yellow Flashing, Drive Stopped : A start inhibit condition exists, the drive cannot be started. Check parameter 214 [Start Inhibits]. Flashing, Drive Running: An intermittent type 1 alarm condition is occurring. Check parameter 211 [Drive Alarm 1]. Steady, Drive Running: A continuous type 1 alarm condition exists. Check parameter 211 [Drive Alarm 1]. But there is nothing about Not Enabled..Also I can not start the drive..I have checked parameter 214 it is Fault but I can not change this parameter. Please help Aleks [/INST] Hi, first of all we have to say Param. 214 is a read-only, so you cannot change it... which of the bits are on in that parameters ?Did you configure a Digital input as Enable ? In that case you have to have 24 volt on it to enable the drive...Did you remove the hardware enable jumper from the drive board? Please check the above and post again the complete reading from Param. 214 to get more help... - fuzzy logic n </s> |
<s>[INST] Open Popup using NetLogic in FTOptix? Hello, all! I am trying to open a popup based on a variables value at runtime. Although, I am having trouble trying to bring this functionality to the project. I can't seem to find any documentations that relates to opening popups/windows using NetLogic. I also tried playing around with MessageBox.Show() and passed in my popup through this, but no luck. Is this something that would have to be pieced together with different assemblies and references outside of Optix prebuilt library? Or am I missing something within the documentation that could point me in the right direction? Thank you! [/INST] Hi Sipes, You should be able to do this using the .OpenDialog() method. In the Template Libraries, you can add the Login form to your project, which will bring in a NetLogic called 'LoginButtonLogic'. If you open it, you'll find a good example of how a popup dialog is called using this method. Hopefully that gives you enough ammunition. Thank you, AutomateSHANE! I will attempt this and see if I can get the functionality out of it! Hey, Sipes. Please let us know if you are successful! Thanks, Eileen n </s> |
<s>[INST] FTView SE Trending I'm looking for a way to load a set of pens to a trend using a pushbutton. Does the trend object support loading preconfigured trends from saved files?In other HMI packages I am able to configure a trend with pens, time span, start time, everything and save that configuration. Add a button to a screen that when clicked at runtime will load the prconfigured trend definition file to the trend object. I've looked at what's available and see nothing of this sort. I thought Templates might be the trick but am not sure how to configure pens for a template. Also, tried to save a test template and load it during runtime with no visible results. Any ideas? [/INST] Yes, you can use trend templates. Create your trend (pens, span,...). Then, in Trend properties (Template Tab) you can select which properties to save in template. With right selection of propertis you can create button command only to change trend's time span or what ever you like. And finally assign the command to button action:Invoke Me.Trend1.ClearChart Invoke Me.Trend1.LoadTemplate(YourTemplateName) This is all assuming you already have a trend set up to show live data: To get a trend to show historical data, you will need to set up a Data Log Model in FTView to store the data on your server. In order to get a trend to show historical data, you must set the trend properties as follows: General Tab: Data Server --> Poll Historical Data Pens Tab: Change the Model of your pens to the Data Log Model you created. To start the data logging run the command DataLogOn mydatalogmodel n </s> |
<s>[INST] ControlLogix Data Storage Options Summary: Alternate Ways To Store PLC Data I have a ControlLogix L73 that is being used to collect various data information from HMI and an Oracle database. The information is then used throughout the process between multiple stations. The requirement suddenly grew quite large and we are running out of memory in the processor. Aside from going up in processor size, is there any other alternative I can look at? [/INST] You should look into FactoryTalk Transaction Manager, or FactoryTalk Historian. We have transaction manager in the project, but the client doesn't want to do the data storage in their existing Oracle database or run all the data across their network. We have suggested installing a separate database in a local computer on a separate network, but that means someone has to maintain the database and they didn't like that. https://www.rockwellautomation.com/rockwellsoftware/data/historian/historianme.html That link points to FT Historian ME - it's a Controllogix module so their beefs about managing another computer are covered. Never mind that it is effectively another computer; if it's in a Controllogix card form factor, it's PLC hardware. Take a look and see if that suits your problem. n </s> |
<s>[INST] RSLOGIX 5000 software Edition selection Summary: Correct software edition selection help for L32E contoller I would like to purchase RSLOGIX 5000 software for compact logix L32E controller , the vendor give me the quote for Mini and Pro edition , Mini version can only be used with the Compact Logix PLCs and exclusively in ladder logic language. Will this version support compact Logix L32E controller for upload/ download software and trouble shooting application . I would like to make sure the compatibility prior to purchase the software all help appreciated in advance [/INST] Welcome to the Forum ! Mini Edition will support your controller, until version 20.xx (L32E hardware doesn't allow a firmware >v20.xx). If you would like to use other programming languages, you may buy Lite Edition instead, or just buy an additional language you want your software to support. I suggest to take a look to the following web page: http://www.rockwellautomation.com/rockwellsoftware/design/studio5000/orderinginfo.html - fuzzy logic In order to enhance the reputation of the Forum's contributors, please rate the replies you got and remember to close the thread clicking Choose as Best Answer button over the solving answer. Thanks ! n </s> |
<s>[INST] data logging in Micrologix 1500 Dear Sir,I am doing some project involving data logging using ML 1500 and RSVIEW32 and RSlinx etc. I want to know if the PC is not switched 'ON' for some reason then can the data be retained in PLC itself and data downloaded when PC is switched ON. And if yes then for how long? thanks ragni [/INST] if any help for this , will be great ragni ragni, answer could be yes...just I think it is not so easy to realize... :smileysad: You can try to use the data logging functionality inside micrologix,starting to log when PC is switched off; in Aid 18498 there is a quick start doc that helps on configure it. After that, in order to retrive informations logged, you have two ways: 1. using the Data Logging Utility, that creates a .csv file with your data2. creating your own software application inside PC, following the instructions you may find in chapter 22 of Micrologix Instruction Set. About your question on how long the data can be retained... Datalog memory is 48Kb, retained by battery... so the data can be retained until battery is ok... If you're referring insted to how long I can log data before reach the memory limit, then it depends on how many data you want to log and with which frequency... Hope this helps.... - fuzzy logic n </s> |
<s>[INST] Drive executive and Kinetics 6500 over ethernet Summary: Drive executive and Kinetics 6500 over ethernet communucaitionDoes Drive executive work with Kinetics 6500 servo drives over ethernet with RSLinx? [/INST] I just opened it and tried to create a new file - K6500 is not an option. While you could access a PF755 drive which is controlled via CIP motion from a logix processor, any changes you could make to parameters are wiped out at the next power cycle. Drive Executive is not intended to work well with CIP motion hardware. n </s> |
<s>[INST] [Help]FactoryTalk View Can't Communication Summary: NULL ??????????,????FT View????/????,?????/?? ??,??Rslinx????,??Logix Designer????? ???????????? FactoryTalk??11 RsLinx??4.21 Logix Designer??30.01 [/INST] Welcome to the Forum ! First of all I suggest not to use chinese ideograms in asking and describing your needs... otherwise the chance other users here can help will dramatically reduce. To be able to communicate from PC to Panelview Plus and Logix Controller, you should define an Ethernet driver inside FactoryTalk Linx. FactoryTalk Linx --> Communication Setup --> Design (Local) --> right button on the first line and Add Driver --> Ethernet This should let you add a new driver with auto-browsing capability, so that you can discover your devices on the network, as in RSLinx Classic. Probably other steps would be needed, but I suggest to start from this one and let us know. You can also follow this technote: QA4847 Hope this helps, - fuzzy logic In order to enhance the reputation of the Forum's contributors, please rate the replies you got and remember to close the thread clicking Choose as Best Answer button over the solving answer. Thanks ! – / 1 n </s> |
<s>[INST] Using a 842-CM-MIP3BA Encoder to perform a follow Summary: Sample code req to create follow with encoder.Hello All Hopefully somebody out there has already performed this and may have some sample code. I am using a 842E-CM-MIP3BA Encoder to Follow a press. The encoder drives a motor that is installed in an off line m/c(( the motor is controlled from a 2198-H040ERS2 Drive)& the motion is controlled from a 1769-L18ERM-BB1B CONTROLLER)). I have Studio 5000 ver32.(I,m new to this so still learning) All I simply want to do is drive the motor from the encoder and if required change the motor direction and follow ratio. Any help would be appreciated guys. [/INST] Congratulations - you correctly selected a CIP motion Ethernet/IP encoder. It's very easy to NOT get it and you would not be able to take advantage of it in CIP motion. The encoder will be a CIP motion axis and you can issue a few commands to it, such as MAH and MRP. MAH only works if the homing tab of the axis is configured to be immediate. The axis can then be used as a master axis for camming or electronic gearing. In your case, it looks like MAG (motion axis gear) would work well. While it's a somewhat simple application, CIP motion is not all that simple. There's a lot to motion, more than can really be answered in a few forum posts. If you have a good local Rockwell representative or good Rockwell distributor, they should be able to spend an hour to help get you started. Thank you for your reply, it gives me a good start and direction. Kindest regards Scott n </s> |
<s>[INST] Using Non AB Absolute Linear Encoder with 1769 platform Hello All! I am using a 1769-L36ERMS contoller for an upgrade to an old machine that utilized ABSOCODER Linear encoders for position read-outs. My delima is that the encoders were previously connected to a signal converter in order to be used with the existing control. I would like to us these encoders if possible with the AB controller and possibly leave out the signal converter. The encoder and signal converter sites are below. I can't decide if I need a 1769-IQ16F or the HSC card. Any insight? Thanks! Encoder PN: VLS-256PW Signal Converter PN: VM-2A-16 https://www.artisantg.com/info/NSD_VM_2A_32_Manual_2020108163020.pdf https://www.nsdcorp.com/product/line_sensor/vls/index.html [/INST] Hi Kurt, The ABSOCODER encoder is an absolute encoder. The VM-2A(MRE) is a signal converter that takes the raw signal from the encoder sensor and converts it to a 16-bit binary (or 16-bit gray binary) driver signal that can be consumed by a digital PLC input module. Unfortunately, this converter is required in order to use the sensor. In this case you would need the 1769-IQ16F module to read the output from the converter and then have programing code to evaluate the position based on the signals. See: Understanding Absolute Encoder Output Types (custhelp.com) for further information on absolute encoder signals. n </s> |
<s>[INST] RSlogix 5000: Alarm (ALMD / ALMA) Hello, I would like to know how I can extract (use) to text of an ALMD or ALMA instruction. The idea is to send it to an Inview. Best regards Hep [/INST] You cannot programmatically access the alarm message string from the alarm tag. Anyway there is a workaround... try to see Aid 57602.... Hope this helps… - fuzzy logic Hello, why not. But it did not help for the creation ..Let me thnik about it. ThanksHep Hello, I'm using the ALMA but I need that the HH and LL alarms need reset to back to the normal. Is this possible with the ALMA block? n </s> |
<s>[INST] factorytalk vantagepoint, factorytalk historian Good morning, excuse me, someone have information about the software`s FactoryTalk VantagePoint / Historian. Some User Manual or information about how work with them. [/INST] Literature for Rockwell software can be found here! https://www.rockwellautomation.com/nl_NL/literature-library/overview.page Hi All, When i open vantagepoint Manager & Portal page, error page shown. kindly help to resolve this. Regards, M.Arunkumar n </s> |
<s>[INST] Vantagepoint - Report Publish Error Summary: Unable to publish excel report via Xcesius Hi, I'm a first time user of Vantagepoint and Xcelsius. I have created a very simple dashboard report in Xcelsius to show two guages to represent tank level. I have configured Xcelcius setting for publishing following the help file instructions. When I try to publidh the report I get the following error messag: Failed to create the requested report template. Object reference not set to an instance of an object. Not sure how to get around this issue, I suspect I've missed a step somewhere. Please advise... Justin [/INST] Hi Justin, welcome to the Forum ! I really don't know Vantagepoint... I think you should post more infos about software version and OS in order to get help. Anyway, I suggest to take a look to the following technote: 59530 - FactoryTalk VantagePoint Patch TOC You could find either a patch or an update that solves the issue. - fuzzy logic In order to enhance the reputation of the Forum's contributors, please rate the replies you got and remember to close the thread clicking Choose as Best Answer button over the solving answer. Thanks ! n </s> |
<s>[INST] RS 5000 V17 Lockup when pasting online Has anyone had this bug happen in V17. During an online edit, a couple of bits in one rung need to be copied and pasted in another. After the copy, a paste is attempted in another rung, if enabling edits on that rung were skipped, as soon as the paste initiated, the software locks up, and eventually shuts down. V16 and earlier dose not seam to have this issue. [/INST] Do you get an error message ? Which one ? Usually, there is a file where the Fatal Error is logged, at he following path: C:Documents and SettingsAll UsersDocumentsRockwell AutomationRSLogix 5000LogsRSLogix 5000 Fatal Error.Dmp These informations could be useful to try to help you... :smileywink: - fuzzy logic n </s> |
<s>[INST] RSNetworx for DeviceNet [Read Only]? Just installed RSNetworx for DeviceNet and when I try to run it, it comes up as Read Only.Operating System is Windows XP Pro SP3.I have heard that there are issues with some software using SP3. Are there any alternatives other than uninstalling SP3? [/INST] Update on my previous message.Both RSNetWorx for DeviceNet and Ethernet give me the same message.If I try to use it, a pop up window says 'RSNetWorx could not connect to Factory Talk Directory. Contact Rockwell Automation Technical Support for more information.Another guy here is at SP2 and is getting the same message.We have one guy that is able to run it with no problems, and one other that is still at version 8. Could this be something in Factory Talk instead of RSNetworx? There are some issues on FactoryTalk security and RSNetworx... See Aid 35763 for CPR7 or Aid 47136 for CPR9 Anyway, XP SP3 is not supported at this moment...:smileysurprised: Hope that helps... - fuzzy logic Thank you for the feedback!When the checkbox for security came up, it was not selected. On all other attempts of uninstalling and reinstalling, I don't recall ever checking this box. It is now coming up properly, so I must have selected that at some point.Appreciate the assistance. Great ! And many thanks for your positive feedback. :smileyhappy: - fuzzy logic n </s> |
<s>[INST] FTView SE V11 Google Chrome web browser I am trying to use Google Chrome browser instead of the IE within FTView SE Environment. any one knows how to do this?. is it even possible? [/INST] nan n </s> |
<s>[INST] Micro820 - can't connect anymore Summary: After downloading MQTT sample code I can't connect to my Micro820 anymoreI have Micro820 and it was working fine until I downloaded MQTT sample code to it. After that I can not gain access to the Micro anymore. I tried over DHCP and connecting it directly by ethernet cable to my windows 10 computer. I tried discovering the Micro with ipconfig and and arp -a but with no success. Status of the Micro is: enet led is green on, run led is green blinking [/INST] Welcome to the Forum ! If you cannot either PING it, it can be locked somewhere due to an internal error... You could try a reset to default procedure, (firmware upgrade) see QA30209 Here some technotes that could help on downloading firmware: QA15715 QA9802 QA19126 - fuzzy logic In order to enhance the reputation of the Forum's contributors, please rate the replies you got and remember to close the thread clicking Choose as Best Answer button over the solving answer. Thanks ! Hello, Thank you for your answer. Since I have Micro820 I believe it does not have USB port so the only way to do firmware upgrade is via ethernet but my problem is that I can't find my Micro820 anywhere on the network. How can I perform firmware upgrade if I can't connect via ethernet? You can try through the SD card. Please follow the indications you can find inisde the User Manual, app. C Hope this helps, - fuzzy logic In order to enhance the reputation of the Forum's contributors, please rate the replies you got and remember to close the thread clicking Choose as Best Answer button over the solving answer. Thanks ! Thanks for the tip. I followed those instructions but to no avail. I am not sure if firmware upgrade or downgrade is really happening. What I get is a SD led blinking for a brief period at the startup of the Micro820 but I do not get any run/fault light blinking as is explained here: https://rockwellautomation.custhelp.com/app/answers/answer_view/a_id/1060515 I also tried setting IP address via ConfigMeFirst.txt and still can't ping my Micro820 I also tried making backup of the current project with [BKD] ConfigMeFirst.txt command but again nothing happpens. This is a long shot, but use an Ethernet discovery app such as WireShark or Advanced IP Scanner (my personal favorite) to find the IP that the Micro820 is currently using. Make sure that the Micro820 and your programming computer are direct connected, and isolated from all other Ethernet devices. If you find an active IP, it should be the Micro820. If you don't, you may have a hardware issue. Did you check the IP address for 820 got changed after the sample code download? You can check what IP address was set in your project. Alternatively, you can use sd card to configure the IP address. Since V12 most of the SD cards are not working anymore. You have to us the Rockwell SD card (2080-SD-2GB). When the SD led is not on after you put in the card, the SD is not working with the Micro! n </s> |
<s>[INST] Translation In Siemens STEP 5 or STEP 7 programming software, the method of representation for programming language such as Ladder Diagram, Instruction List and Function Block Diagram is translatable with each other by the software. Is RSLogix 5000 capable to translate Ladder Diagram, Structure Text and Function Block with each other similarly? [/INST] No, there isn't this possibility. The Languages in RS5000 are to be considered complementary each other, giving the possibility to use the best language to realize your needs... for example if you have a sequential machine, you will find that SFC is the right choice.Or, if you want to control some process, you will find special instruction in FBD... - fuzzy logic In case you are trying to evaluate one against the other I add this. Step 7 programming is mainly equivalent to Ladder Logic and they just have different ways of viewing the same logic. The Structured Text, Function Block (and SFCs) in RSLogix 5000 are quite different. You would have to look at PCS7 to see something similar in the Siemens world. It does not switch views between these programming languages either. n </s> |
<s>[INST] Power Flex 700 scr pre charge board We have a AB Power Flex drive, P/N 20B D 096 A3 ANNANCO, that we lost the precharge board, P/N SK G9-PRE1-V480 (long story) and I am told by my local dist and Rockwell that it is a 10-15 day lead time. My question is do the other 700's have the same precharge board or are they specific to drive size? Thanks in advanceDave [/INST] Yes, the 400 / 480 Vac versions of all the PF700 have the same Precharge board (starting from frame 5), as you may see in the Spare Parts listing.... Hope this helps… - fuzzy logic n </s> |
<s>[INST] ALMD (Alarm) in a ADD-ON Instruction? Señores,Quisiera saber si hay alguna complicacion en colocar una instruccion ALMD dentro de un Add-On instruction. Segun una ultima charla con personal de Rockwell nos indicaron que esta version (16) no estaba preparada para eso. Sin embargo las Alarmas funcionan. Can I place an ALMD Instruction inside a Add-On Instruction? [/INST] Yes, you are now supposed to be able to put any reasonable (non controller type) function blocks in the add on instructions. You will need to create the appropriate local parameter to support the ALMD (just like if you put it in a standard routine). vlk Per the AOI user manual (1756-PM010A-EN-P), the ALMA and ALMD instructions CAN be used in an AOI, but the backing tag for the instruction must be passed as an In/Out Parameter. Same for MSG and Motion instructions. This is because the MSG, ALMA, ALMD instructions require BASE tags (root controller tag or program tag) and have an associated buffer space in memory. Can't put them in Arrays or as parts of UDTs. Dale BTW, the manual above is installed with the online manuals, but it's not easy to find. Select the Common Procedures Programming Manual and you'll get what looks like a manual Cover Page, but it's really links to several other manuals (AOIs, Strings, P/C Tags, Messages, etc., etc.) Thanks W8ABZ... people from rockwell told me that this last version (16) was no released or prepared to support this, and i thinked: that information is wrong.My mistake... i didn't see that manual n </s> |
<s>[INST] RSView32 7.4 & RSLadder5 Issue I am trying to use the RSLadder5 version 5 ActiveX control in an RSView32 version 7.4 (CPR9) application. I have followed the steps in the manual, but everytime I try to accept the properties window after selecting the .RSP off-line file the RSView32 software crashes with some type of memory exception. I searched the KB but nothing turns up. Any ideas? [/INST] aiki, I guess you've already solved it... :smileytongue: Anyway, if you've not solved this issue.... did you try the patch indicated in this Technote ? Aid 33749 - fuzzy logic I did get the issue solved, although it was with another tech note. But thank you for the follow up. n </s> |
<s>[INST] azerty keyboard in RSLogix 500 OMG!!!! Please can some one tell me how to set keyboard on AZERTY mode in RSLogix 500 :smileymad: Thanks! [/INST] Sacre bleu ! RSLogix 500 has no awareness of keyboard layouts; that's purely a Windows operating system setting. Are you encountering an issue with hotkeys, or descriptive text ? Are you running a localized version of Windows, or a standard Windows installation with an input method editor ? n </s> |
<s>[INST] Modern RS Messenger? So it looks like Messenger is slipping slowly into legacy status along with RSView32, with FactoryTalk being the replacement. Is there a messenger equivalent for FactoryTalk? Does it have the capability to send voice or text via a phone line? [/INST] Nothing new in the works from Rockwell, but Spectre Instruments makes Win 911, which has improved Dialogic support. Tech note 52456 has a link to their web site, which is http://www.specterinstruments.com/ Win911 works with with RSView32 and SE, so I don't forsee any major developments from Rockwell to irev Messenger. I agree with you, Messenger is basically in a maintenance mode. n </s> |
<s>[INST] CompactLogix Ethernet Gateway Problem Summary: Ethernet comms lost because of invalid gateway?Hi, I had an issue with a compactlogix PLC last night and I could use a little advice if anybody has seen this before. I was asked to change the IP address of a 1769-l32e and local HMI which were set for a private network to settings which would allow connection to the factory network. The settings I was given to put in were :- IP 172.16.4.14 sunbet mask 255.255.240.0 gateway 172.16.255.254 After getting these settings in via linx and establishing communications ok with the HMI everything looked good, however after power cycling the machine the PLC lost it's CIP connection to the HMI and linx. I could still ping the IP address ok but could not connect and the NS light was solid red indicating a duplicate ip which was not the case. (even disconnecting the PLC from the network and rebooting it would cause the same conditions. The only way I could reconnect to the PLC was to run bootp and reset the IP address to what it was already set to. I was quite surprised to be able to see the bootp request because bootp and DHCP were both switched off in the PLC configuration. I eventually managed to stop this happening by removing the gateway address completely. [/INST] .255 is not a valid IP address octet for a gateway. I think it got typoed Thanks, yes I had eventually come to that conclusion. But the nature of the fault surprised me a little. There were no error messages when setting the address and as this can be done online, the PLC was initially communicating with the HMI on the new address without problem. It was only after a power down that the problems started. Then it lost all CIP connections, even those on the local subnet. I would have expected that a bad gateway address would only affect those connections which required the gateway. Also the NS led was red which according to the manual only means that there is a duplicate IP address, it looks like this also comes on for a bad gateway address? I had a similar problem today then the HMI was still connected technically but, no faults would show up on the screen. When looking at the PLC the NS LED was red (duplicate IP address, all of a sudden). I had to switch ports on the gateway to make the PLC and HMI happy but, when I PINGed the gateway it would respond while plugged in one port but not the other 2 extra (timed out). All 5 gateway ports should be configured the same... Just wondering if anyone else had similar problems/ answers/ best guesses?? CompactLogix L30ER Siemens gateway SCALENCE XB005 n </s> |
<s>[INST] How to connect two PV300's to a MicroLogix 1400 Somewhat confused as to how to do this. Any suggaestions. Thx. [/INST] At first it would be interesting to know the PV300 model you have (catalog number)... Then, there could be different solutions, for example: Connect every panelview to a serial port of MX1400 (it has two) Connect both panelview to a DH-485 network using 1761-NET-AIC, and use a serial port of the PLC with this protocol Connect both panelview to the Ethernet network using 1761-NET-ENI, and use the Ethernet port of the PLC As you see, there are different solutions (and also other connections are possible), but the first selection to made is related to the protocol installed on your panelview. - fuzzy logic I'm using the 2711-m3a19l1.One is local to the control panel and the other is remote.No Ethernet is used.DO I need 3 AIC modules, one for each P and one for the ML? Thx, Mark No, Micrologix 1400 side could just use a 1763-NC01 cable instead. You can connect a MicroLogix 1400 controller to your RS-485 network directly without using an external optical isolator, such as Advanced Interface Converter (AIC+), catalog number 1761-NET-AIC, as shown in the illustrations below, because Channel 0 is isolated within the controller. See User Manual - page 81 Hope this helps, - fuzzy logic n </s> |
<s>[INST] Asset Centre and change domain Summary: Domain server was change on existing FTAC systemHi, I changed domain server today. On another machine is/was running FTAC server. In FT directory are only domain users. I tried to specify again FT Directory location, again used FT Dir wizard, through FT Administration console I can see all users and computers. Application didnt start because of problem on the picture. Could anyone help? Thanks ============================================================================= Hello... as you can see on picture, problem was with connection to SQL db. Reinstall of SQL2005 solved this issue and not spend several hours on 'Google' what is it 'error 40' ... [/INST] nan n </s> |
<s>[INST] Downloading to controller hangs in CCW Summary: Cannot get ccw to download to either 810, 830 or 850 Hi, I have recently installed CCW and am experiencing an issue with downloading project to controller. I am able to communicate with the controller in every other aspect, eg upload, flash etc, however after building project and then downloading the download hangs endlessly. i have disabled all firewalls and antivirus programs, uninstalled and reinstalled ccw, however issue still persists. I have also tried with both standard and delevoper versions of ccw as well as with supplied package is RSLinx and even with a RSLinx Lite. Computer is running Windows 7 32 bit. has anyone else experienced a similar situation? [/INST] I can't download either. I get an error that says: Download failed or was interupted by a lost connection. but it actually never loses connection. I tried most of the things you tried also Craig, what I did to resolve my issue was to load CCW onto a 64bit machine and then I had no further issues. Previously I was using a 32 bit machine Wow - Is this the fix? To load CCW onto a 64 bit machine??? What if we don't have a 64 bit machine? Are we dead in the water? n </s> |
<s>[INST] 1734-AENT Adapter losing connection with its controller. Hi everyone, I'll try to describe the issue I am having in the best way that I can (english is not my native language and I apologize in advance for that). I have a subnet on which I am running a mix of 1734-AENT and 1794-AENT adapters with a CompactLogix 1769-L33ER controller. The issue I am having is only with the 1734-AENT adapters (I have a total of 3), they all seem to lose their connections randomly. I would lose the connection on only one, two or even all three of them. I haven't had any problem with the 1794-AENT adapters so far. What I mean by losing its connection is this: The network status and Pointbus LEDS on the adapters are blinking red which, after researching, seems to indicate that one or more I/O ethernet connection(s) has timed-out and that a recoverable fault has occured because of a node fault. On all the cards attached to the adapter (1734-IB8, OW-4), the network status LED are blinking red too. Again, seems to be pointing at an I/O connection that is in a timed-out state. When it happens, a power cycle of the faulted adapters put them back online and working. When the problem occurs, in the PLC status register of the faulted adapter I can only see that it is faulted by having a value of 16 [/INST] Check your RPI settings. I had an L35E that would lose connection with various drives and 1794-AENT I/O. When the system was installed, the RPI settings were set to 1ms on everything and the controller was flagging communication errors until it just refused to communicate with anything until the system was power cycled. Once these were defaulted back to 20ms, we haven't had any issues. Hi, I checked the RPI for all the 1734-AENT and also all the 1794-AENT, they all have the RPI set to 20ms. But, the RPI for the ethernet card (1756-EN2T) on the controller backplane is set to 10ms. I could try increasing it to 20 ms aswell and see if my problem still occurs. Thank you for your response. Actually, I was wrong the ethernet card 1756-EN2T is not on the 1769-L33ER backplane but it is on the backplane of another controller with whom the 1769-L33ER is exchanging data. Morneau Verify you have not exceed 32 EtherNet/IP connections for the 1769-L33ER. (see p7) Consider upgrading the 1734-AENT firmware from v4.003 to v5.019 because there are known issue as seen in the release notes ID: BF20959 | Access Levels: TechConnect 1734-AENT/1738-AENT adapter: Error 16#0203 - Connection timeout Hi Philip, Just to be sure I understand this correctly, to verify the number of ethernet/ip connections on the controller, I have to count the number of devices connected to it in the controller organizer using a rack optimisation connection? Maybe there is a better way that I do not know. So a drive, an ethernet card (for a HMI) and any type of adapter (1734 and 1794) would use 1 connection each ? Data transfer between two controller would count as 1 connection since it is a connection between two ethernet card ? For instance, a 1734-AENT adapter with 6 cards on its backplane would count as 1 connection and not 7 ? (I think it would be 7 only if using a direct connection instead of rack optimisation connection, but I may be wrong). Following this idea, the limit of direct connections for this controller model would be 256 as stated in the document that you linked ? Excuse me for being quite new to this, I'm trying to learn it right ... If the controller has more than 32 connections, is it fair to assume that it would fail to communicate on more than just the 1734-AENT adapters ? I'd get some errors communication with the drives and the 1794-AENT adapters aswell at random ? I'll try upgrading the firmware of the 1734-AENT adapters and see if I still get the issue. Thank you for your response. Morneau 32 EtherNet/IP Nodes = 32 IP addresses in the IO tree I think it's better to clarify a little bit about connections, in order to avoid creating confusion and misunderstanding. The limit for the -L33ER controller mentioned by Philip is actually the maximum number of supported EtherNet/IP Nodes, not connections. Ethernet/IP Network node limitation has been created as a simplified way for selecting a controller. Nodes on an Ethernet/IP Network is the number of devices that you can add into the Studio 5000 Logix Designer I/O tree of a project. The word connection is instead typically used in our manuals to specify the maximum supported CIP and TCP connections: Basically, each device (Node) on the network uses 1 TCP connection and 1 (or more) CIP connection. As you can see from the table above, the -L33ER controller supports up to 256 CIP connections. It is a limit that should still be consedered when sizing your applications, despite it is higher compared to the maximum supported Nodes; it depends on the type of device you have on the network: a drive typically uses a single CIP connection, but a 1734-AENT adapter can use more, based on the mounted I/O modules and their communication configuration. More recent Studio 5000 versions will check if the EtherNet/IP Node limit has been surpassed when you Verify the project and the Download isn't permitted if you configured more than the supported Nodes. Older software version didn't instead throw an error for that limit, so there can be cases where you cannot be aware of it. So, in this case, just start counting every device you added to the I/O tree in your project against the maximum supported EtherNet/IP Nodes for your controller (32). Which is basically what Philip suggested. n </s> |
<s>[INST] TLS-1 GD2 440G-T27121 with release switch .step model Summary: Need a 3D step model for design purposeHi, I just cant seam to find what i am looking for, I need a 3D step model of a TLS-1 GD2 (440G-T27121) lock with release switch mounted. [/INST] Welcome to the Forum ! As far as I can see, the only available drawings are here: QA7651 If it is not enough for your needs, you can try to ask, following indications from IP214 Hope this helps, - fuzzy logic In order to enhance the reputation of the Forum's contributors, please rate the replies you got and remember to close the thread clicking Choose as Best Answer button over the solving answer. Thanks ! n </s> |
<s>[INST] Blocking of User Account on a PVPlus terminal after a number of wrong entries Is there any way to block an account on panelview plus terminal after a particular number of login attempts fails (wrong password) Just like in a windows PC? [/INST] As far as I know, no way... there isn't VBA code in PVP, there aren't particular functions tied to the login window to chech for failed attempts... - fuzzy logic I think rockwell should think about thisBecause, entering a password on the popup keyboard is visible to others, and anybody can access anything thanks for the reply If I'm not mistaken, any login box for username and password displays the password as '*' for every character. Are you using a string input in place of a login button? n </s> |
<s>[INST] NoFields Summary: PanelView 5500 Screen saverHow can I change the screen saver on Panel View 5500??????? [/INST] Welcome to the Forum ! As far as I know, actually it can only be enabled or disabled. - fuzzy logic In order to enhance the reputation of the Forum's contributors, please rate the replies you got and remember to close the thread clicking Choose as Best Answer button over the solving answer. Thanks ! n </s> |
<s>[INST] Setup Powerflex 40 in Connected Components Workbench (CCW) Summary: Initial setup of Powerflex40 drive using USB to RS485 converter and CCW.How do I connect the Powerflex 40 drive using RS485, and set it up in Connected Components Workbench (CCW). I don't see instructions in the users manual. I see there are various add-on modules, but I just want to use a USB to RS485 converter, and splice it into the RJ45 jack. How do I get CCW to discover it using Connection Browser? I went to Configure Drivers, and I don't know if I should use 1784 PKTX(D)/PCMK for DH+ and DH485 or DH485 UIC Devices or another one? Do I need to setup anything on the drive first? Thanks, Greg Windows 10, CCW version 12.00.00 Standard [/INST] I see the users manual is saying you can use Drive Explorer application, but I think RA wants everything to move to CCW. Nevermind, I just set it up through the front panel, would be nice to know for future reference, but this issue is resolved. When you say USB-485 converter, do you mean an Allen Bradley 1747-UIC converter? That shows up in RS-Linx and I think it would work to talk to a drive using CCW. I used a HMS anybus 7007 to connect with PowerFlex4M, , BUT the stutus register is always NOT ready Meanwhile , it can not be recongnized by CCW.. i don't know what happpens By the way , suggest you install a 22-comm-E with PF40 , it should be working . A 1203-USB is what you would normally use to program most Rockwell drives via serial port. The 1203-USB comes with a cable for DPI as well as a separate cable for the RS485 compatible drives. You add the 1203-USB to RSLinx and you should be good to go. n </s> |
<s>[INST] Clearing a Micrologix 1100 fault. Is there a way to clear a fault in a ML 1100 without using a PC connected to the PLC? Thank you! [/INST] elrg, you want try to cycle power to it (old good method :smileytongue: ) but I think there are little possibilities to solve... if the error is still there, the controller will fault again :smileysad: First good info is to know the status of the fault led: if it isn't flashing, but solid red,then it is related to an hardware issue, and maybe impossible to clear that fault. Only hope is that the fault is caused by an accumulated value become too big, and that a startup routine will clear it at powerup. I think unfortunately that the best solution is to have somebody connected to the plc to see which is the error code, removing the cause of fault and restart it. - fuzzy logic n </s> |
<s>[INST] FactoryTalk Directory on Redundancy Hello Fellows, In FTView SE redundant system, how can I set up FT directory of each server (Primary & Secondary) ? I made Primary server as 'Local Host' and Secondary server as remote (look up to primary server's directory).Is it right ? [/INST] Try to take a look to Aid 58803, there are informations and hints about the best Network FTD practices. See also the User Guide - chapter 4, and Aid 32549 - Aid 40891 for complete reference. Hope this helps… - fuzzy logic There is no redundant FactoryTalk directory per se, but each box caches a copy of the FT directory locally. Therefore, it is not necessary for there to be a redundant FT directory. The only thing that happens if it is not available is you cannot make changes to the project until the FT directory becomes available again. We run an SE system with 5 pairs of redundant SE servers on a single FT directory. My experience is that when the factory talk directory server goes dowm, the SE servers also go down, or at least take a big know. I know that this is not supposed to be the case, but for some reason or other the SE servers do not switch to the local FT directory. For a redudnant pair, both server point to the same remote FT directory server. If we use a local server, as we do from time to time when upgrading software revisions etc, we designate one ofg the servers as the FT directory server and set it to local, and the point the other server to this server. My question is that for redudnant servers, if both point to a remote FT directory server, and this goes down, they will then each use their local directory. Is this feasible on a redudnant system, as they surely use link to the same FT directory to determine who is the active server? We may well have got the config wrong. We are taking it up with the help desk, but would appreciate hearing from others who have large multi-server systems with redundant SE servers. Steve Steve, if the servers lose the connection to the FactoryTalk directory, they each will use their own local cached information. These are the files that exist in C:Documents and SettingsAll UsersApplication DataRockwellRNAClient and below. Hope that answers the question. My question is that for redudnant servers, if both point to a remote FT directory server, and this goes down, they will then each use their local directory. Is this feasible on a redudnant system, as they surely use link to the same FT directory to determine who is the active server? Yes, not only is it feasible, but it is recommended. The FTD doesn't determine who is active, per se. It provides the path to server locations; HMI services on the servers themselves determine who is healthy and active. See AID 66352 - FactoryTalk View SE Behavior when FactoryTalk Directory is Unavailable The functionality of the application (i.e., what you can and cannot do when the FTD is not present) is the same regardless of whether or not redundancy is enabled. Furthermore, this AID will be updated within the month to document that the loss of a FactoryTalk Directory does NOT bring down HMI (or any other) servers, even if redundancy is configured. One good way to troubleshoot what your servers are doing is to add this screen to your application. Once you configure it, you can see all server statuses on a client screen. AID 44624 - FTView SE 5.0/6.0 - Determine a server's currentstatus and state using VBA display code n </s> |
<s>[INST] Migration 1746-IN16 to a compactlogix system Summary: 24vac input in compactlogix systemHi there guys, i need to migrate a SLC 5/04 system to a compactlogix system, i have a problem with the io because in the plant i have right now 56 module Honeywell S87B1016 to control a oven for bread, this module have one output to indicate a ignition of a flame in 24 VAC (i need 56 input in 24 VAC) if anyone know which system of i/o can i use. i really be grateful to let me know. i think to use a relay with a input in 24 VAC but i think this is not a adecuate solution because i adding a point of failure in the system which could eliminate by placing a suitable io system Thanks for the time guys. [/INST] Welcome to the Forum ! As far as I know, there are no chances to have this voltage working on I/O modules from RA (Flex I/O, Point I/O, Compact I/O) - fuzzy logic In order to enhance the reputation of the Forum's contributors, please rate the replies you got and remember to close the thread clicking Choose as Best Answer button over the solving answer. Thanks ! We have some experience with burner control systems; Rockwell does not offer dedicated burner controls. You are likely going to have to replace Honeywell systems with another Honeywell product, especially if you are going to meet safety standards for burner controls. n </s> |
<s>[INST] Can someone share a sample of .vpd project file of Studio 5000 View Designer Is it readable by notepad editor? [/INST] No, it's not. For a collection of examples, I suggest to start from the following technote: QA44040 You can also find other info in the following post from Keith: LINK fuzzy logic Please don't forget to LIKE and highlight the decisive answer: REPLY > Make Best Answer n </s> |
<s>[INST] downsides of running drive at low frequency for long periods? Summary: What are the disadvantages of running a VFD at a low frequency for an extended amount of time? [/INST] The VFD doesn't care what output frequency, it will run anywhere in it's range all day. The problem is the motor. A normal general purpose motor TEFC motor will not cool itself at low speed and burn up windings. you need to know the turn down ratio of the motor. A 4-1 turn down ratio means it will have proper cooling at 25% speed. You can get a motor with a greater turn down ratio OR install a larger motor to help reduce the heat on the winding. I have had to instal larger motor in the textile industry for that very case. Hoped this helped. No down sides from the drive perspective. However, you need to check on the motor side. If the motor is a inverter duty motor , it will normally have a seperate supply for its cooling fan & then you can run it a lower speeds too. Sorry guys, but there IS A DOWNSIZE regarding the drive at very low frequencies. See the attachment. n </s> |
<s>[INST] RSLinx 500 and FactoryTalk Transaction Manager We are in process of setting up a new process using RSLINX 500 and FactoryTalk Manager. Is there a control connector which comes with FactoryTalk or is this a seperate purchase? [/INST] I think you are asking if it is possible for FT Transaction Manager to connect to a SLC-500. If that is the case, the answer is yes. You can use a generic OPC driver to accomplish this. n </s> |
<s>[INST] Factory Talk View Site Edition Summary: Logic and Control (Events) I want to run a macros as per tag values. so I created macros and events and in the events I creates a action for macros and created a expressions for executing the macros. Here event in number -1 is executing but when the value in the tag changes event number -2 is not executing so please guide how to configure and work...... I upload a pdf file which contains the runtime screen where event 1 is executing and event -2 is not executing. and hoe I created event [/INST] Are you able to run the macro from the Command Line ? If it works that way, then try the following: Delete the problem macro from the HMI server project. Recreate the macro and its content Reboot and restart the HMI server. Hope this helps, fuzzy logic In order to enhance the reputation of the Forum's contributors, please rate the replies you got and remember to close the thread clicking Choose as Best Answer button over the solving answer. Thanks ! n </s> |
<s>[INST] PanelView Plus 6 1000 - Trigger tag on any alarm Summary: PanelView Plus 6 1000 - Trigger tag on any alarmHi, Is it possible to set up a tag to trigger on any alarm? I have an HMI project with around 300 alarm message that trigger on various errors. The client now wants to notify the operator with a flashing banner if any alarm is active. I suggested bringing the alarm page to the front as is the norm but he wants a flashing banner on the currently active page. I tried to use a 'Message Notification' tag but I could not get it to work & I dont know any system values I could use in an expression. Any help appreciated. Thanks Paul. [/INST] Nothing that I am aware of. I have done this through the plc in the past by just checking all my alarm bits are off in series to create a all alarms clear bit. On larger projects the alarms are grouped into different areas so one rung does not have 300 XIO's . On newer projects with the CLX I use my own alarm AOI that passes an alarm active ID to the group UDT that the alarm belongs to, then I only need to combine the group alarm checks if a global alarm bit is needed. Wayne n </s> |
<s>[INST] Tag descriptions stored Summary: Are the tag descriptions stored in the processor?Are the tag descriptions stored in the processor or in the .acd file on my PC? If someone else goes online with the same processor from their PC, will they see my tagname description updates or will they only see what they have stored in the .acd file on their PC? (RSlogix ver 20, L73 processor) If you know which publication this is in, could you please include the publication name so that I can share with my co-workers? [/INST] V20 and prior, tag and rung descriptions are stored only in the ACD file on your computer. That's Logix5000. V21 and beyond (Logix Designer if Rockwell's marketing department can convince everyone to start using the term), you can download tag and rung descriptions to the processor. NOTE! This is not automatic! You must check a box on the download dialog box to tell Logix Designer to do this. Thanks TJ. Good to know. Does this also apply for rung comments? https://rockwellautomation.custhelp.com/app/answers/detail/a_id/549501 It includes rung comments. All of the project documentation (routine, program, task descriptions too) get downloaded. The tag descriptions and rung comments do not exist in the PLC - to save on memory. You can write a message in commented out structured text which will reside in the PLC and be viewable by others. So you could have a documentation structured text routine for this purpose. There are some thoughts to change this in the future, but currently these things only exist in the .acd file. That changed with V 21 I was hoping there was a way. Thanks for all the help. We can't go to v21 because it doesn't support redundant processors. How far out is your project due to be released? You might try asking your Rockwell representative when you can expect V21 Redundancy. It must be soon - Rockwell's at V26 now. My project is live. There are three of us that can login remotely and if any of us makes changes, the changes are saved on the users individual laptop (descriptions anyway). Being able to edit the application simultaneously is a terrific feature, but we've found that comments fall by the wayside since they store only in the ACD files. Tim O'Brien's suggestion to use structured text routines to have on-line documentation is probably the best way to go for V20 and older. TJ McDermott Project Manager, Systems Interface n </s> |
<s>[INST] How do I reset Absolute Reference Status I am having trouble with my Kinetix 2000. After a power cycle I can not seem to get my Absolute Reference Bit to reset. How can I do this. I am not sure on the firmware revision but could this be a problem that I need to upgrade the revision to get it fixed? The machine has been power cycled many times before and I have never had this problem. I have a fault set up that will not allow the machine to work but there is no fault on the drive itself. I can work around my fault I set up and the machine runs fine. All values are correct and home is found everytime.... [/INST] MRP or MAH (w/parameters not set to Immediate & Absolute) will reset the .AbsoluteReferenceStatus bit We set up the HOMING parameters as Absolute and Immediate, we still lost AbsoluteReferenceStatus bit (not maintained). We use Tamagawa Absolute Encoder. Do you have any idea? Thank you! n </s> |
<s>[INST] MPL Motor Weight I have searched all over the place, including the motor manuals for the MPL motors, and I can not find the motor weights listed anywhere. I want to use an MPL-A330P-MJ74AA and I simply can not find the weight of the darn thing. Can someone point me in the right direction? [/INST] Hi jdiroff, and welcome to the Forum ! :smileyhappy: Please review the Motion Selection Guide, see page 17 to find the approx. weight for your motor... Hope this helps… - fuzzy logic Thank you very much - I had been looking all over the place. Jim n </s> |
<s>[INST] FT V SE 5.0 GFX files within imported apa not opening I am currently using release number 5.00.00 CPR 9. I have imported a customers APA file into factory talk view studio se. When i try to open some GFX files I recieve this error message. im not sure where to go with it, due to the lack of information. Any advice in which direction to try next? [/INST] Welcome to the Forum ! It seems to be the issue discussed inside the following technote: http://rockwellautomation.custhelp.com/app/answers/detail/a_id/55416 Try to see if helps... - fuzzy logic In order to enhance Forum's contributors reputation, please rate the replies you got and remember to close the thread clicking Choose as Best Answer button over the solving answer. Thanks ! n </s> |
<s>[INST] 1756-ENBT IP address set to 0.0.0.0. Cannot Change Any Ideas? I have a 4 Slot Contrologix Rack that I am using Soly as a Communications Gateway. Slot-0 is an ENBT Card, Slot-1 is a DH+ Card, and Slot-3 another ENBT Card (The Problem Child), Slot-4 is Empty. Slot-0 is on Company Network. Slot-1 ties to all my 5/04's Slot-3 is tied a a New Cell of Machines, Some are in Place and others are yet to arrive. Slot-3 has been working Fine and I have been communicating just fine. All of the sudden everyhting went Dark, so to speak. Module shows Lost Link IP Address is showing up in RSLinx (3.60) as 0.0.0.0 I cannot communicate to it to change the IP Address back and or Reset to Factory Defaults. OK Light is Flashing Green, Link and Net Lights are Off. Any Ideas First of all how this Might have happened and Second How to reset Module to Factory Defaults? IP Address of Slot-0 is Company, IP Address of Slot-2 is Private 192.168. etc Slot-0 and 1 modules are still working just fine. [/INST] Hi you can try this from the manual http://literature.rockwellautomation.com/idc/groups/literature/documents/um/enet-um001_-en-p.pdf page 27 Reset the Module IP Address to Factory Default Value You can reset the module’s IP address to its factory default value with the following methods: • If the module has rotary switches, set the switches to 888 and cycle power. Went thru the Manual l before I posted. Module does Not have rotary switches. Because the IP Address is now 0.0.0.0 I cannot commnicate to it to change anything. Any Other Ideas? The Module is only a few Months Old. Is it showing up in the chassis with RSLinx when you browse the chassis with your computer attached to the ENBT module in slot 0? Does it show up with an 'X' or question mark in its position in the chassis? Have you tried to browse the chassis for that ENBT module by coming in through the DH+ port of youtr DH+/RIO module? If you can see the module in the backplane you should be able to change its IP, Subnet, Gateway addr., etc without having to use the BootP method. My bad, that's indeed only for the new modules! maybe try connecting with boot P program? But if Link lost is indicated, and you are sure its connected to a network. I think the module is broken. and you should contact Rockwell for replacement If it's an ENBT module then it's pretty old as they have been replaced by EN2T's. The only way is to use the BootP-DHCP Utility to change the IP address. Unplug the module and get the MAC address off the side...you'll need this. Install it back into the chassis and if you're connected straight from your computer, you'll need to use a crossover cable. If you're going through a switch, then you don't. When you open the utility you may have to enter the subnet mask (usually 255.255.255.0) and click OK. In the bottom pane select NEW relation list and enter the MAC address, then the new IP address you want to change it to. I have had, on occasion, to do this several times before the module accepted the values. I've also had to pop out the module and insert it back in to get it to accept the new values too. Once you put in the MAC and IP addresses and click OK, make sure you disable the BOOTP/DHCP. Else it will default to this when the module is powered up again. Hope this helps. Yes the Module Shows up in the Chassis and Shows an Active Status. There are No X's or Question Marks on the Module itself. All the 3 PLC's and 2 Panerlviews Under it are shown with red X's No I Have Not tried hooking directly to the DH+ Netowrk and coming in that way. Our Laptops no longer have the PCMK Slots so thats Kind of out. I have a small Gatway that is RS232 to DH+ for me to put my Micrologix 1500's ont he DH+ When I ned to talk to them, I can try that. My RSLinx Gateway 2.59 shows the IP Address at 0.0.0.0 My RSLinx OEM 3.60 Shows IP Address at 255.255.255.255. What is really weird is that if I Right click on the Module and go to Module Configuration it shows that everything is Correct. The red X's are normal in that it can't communication to them through the ENBT. The module won't communicate to anything until it has it's IP address set to the same subnet. You have to use the BOOTP-DHCP utility. Your RSLinx subnet mask should not be all 255's. Configure it to be 255.255.255.0. One reason you're seeing 0.0.0.0 may be the subnet mask is set to zero subnets since it's 255.255.255.255. The Subnet Mask is NOT 255.255.255.255. 255.255.255.255 is what is showing up as the IP address on one of my RSlinx installations. The Subnet Mask is 255.255.248.0 Even still, the subnet mask with the last octet set at .255 will not work. 255 is the broadcast address BUT with the last octet set at 255 you're essentially telling the network that there is no network. Easiest thing to do is make ALL the subnet masks match. this limits the available network nodes to specifically what the subnet mask allows. I do Understand what you are saying But I think you are Misunderstanding My Settings. My Hardware is indeed set to a Subnet Mask of 255.255.248.0 However it is showing up on RSLinx as 255.255.255.255, Via the Plant Network. I do not have a Controls Friendly IT Dept in my Plant or any of my Plants for that Matter. They are all your Typical IT GOD complex Guys and could care less about my Data Acqusition system and Since my System is not required for the Plant to Function I do not have the backing of Management. The Only thing I can come up with is that the IT Dept has somehow Blocked this Module from the Network. Manually Connecting Directly to the Module shows everything is Fine and it Functions Correctly. Plug the Primary Card Back into the Plant Network and No go. RSLinx will never communicate with all octets set to 255. Rockwell's configuration requires that subnet masks be classful. Meaning it must be Class A, B, or C addressing. Class C subnet masks are 255.255.255.0. It does not do well trying to negotiate the network size with your hardware mask set at 255.255.248.0. In RSLinx, go to Communications>Configure Drivers and click on the Ethernet/IP drive you're using and click on Configure. Click the Browse Remote Submet radio button and it will allow you to enter the IP address and subnet mask of the device (PLC, etc) you're trying to connect to and see if that works. n </s> |
<s>[INST] rslinx gateway reverts to lite verison on rdp sessions Hi all, We have setup RS Logix 5000 and RSLinx Gateway on a server running terminal services, so our engineers can remote in to do some work. I know there was an issue with Node Locked FTA and terminal sessions, but i believe we are using the Concurrent FTA. Is there a way to tell which method we are using? If i log into the server at the local console, everything works fine, but if i RDP into the server, RSLinx is running, but you cannot open its window (im assuming this is the lite functionality as i never used lite before). Our licenses are hosted on another server and i have the FTA pointed to the @ipaddress of that server. If i look at the current activations tab, it will populate and shows me 10 in use and 8 borrowed for RSLinx.GW. It is version 2.54. We have 30 seats. Sorry if this has been answered somewhere before, i could only find answers saying to use concurrent activations, and no other details. Thanks for your help. [/INST] Hi bmanning, and Welcome to the Forum... :smileyhappy: I'm summarizing some informations here, and refer to some technotes you may find useful: Will I be able to change the RSLinx configuration/settings (i.e., add drivers, configure topics, etc.) from a connected terminal client?No. Running the RSLinx Graphical User Interface (GUI) is not supported on terminal clients. All configuration must be done on the server computer.[Reference Aid 22923] See also:Aid 33707 - Aid 34135 See Aid 33700 to check settings about your FTA... Some of the indicated technotes require you to enter in your profile the TechConnect Authorization number.... Hope this helps… - fuzzy logic n </s> |
<s>[INST] FTOptix List selector What is the best way to create a list selector that is similar to the one in ME? [/INST] The best way is the one that suits your application the most. However, the most similar way to the control list selector of ME is probably to use the 'List box' object in Optix. Conceptually, they are about the same. Another option is the 'Combo box'. You'll have to decide which works best for your application. The biggest difference is how you set them up. In ME, it is not very flexible. You add the different states explicitly to the control list object and then can just tie some tags to it. In Optix, however, what the list box or combo box controls is up to you. You can point it to a table in a database and have it run queries, or you can point it to an information model in the Optix project and/or in a PLC. The latter is probably the closest to what you are familiar with in ME. An example is maybe more helpful. I've used a List box for product selection (recipe selection, if you will). In the Model in my Optix project, I have created an object called 'Products'. It consists of 10 instances of another object type I created, called 'ProductConfig'. Said object has a few variables. Each variable is linked to the corresponding PLC tag in a UDT. You may be able to tie the List box direct to a UDT in the PLC and remove the Optix model object from the equation altogether. I just have not experimented with that yet. In the List box properties, the 'Model' property is bound to the 'Products' object of my project. Rather than the List box displaying 'Product1, Product2, etc...' I want it to display the name of that product from a string tag in the PLC. That would be the 'Name' member of my UDT. So you see in the 'Display value path' the binding is to the 'Name' variable of the currently selected item. The {Item} is a pointer which is automatically generated by the List box object, which points to the currently selected object. In this example, if the third item in the list were selected, then {Item} corresponds to 'Product3' of the 'Products' object in my model. That means the list box will display what is in the string of the PLC tag tied to Product3.Name. See the light blue link to that PLC tag here: Similarly, you see 'Selected value path' is bound to a variable I call 'Index', which I have explicitly assigned in the model. This tells the List box object the value of the currently selected item, similar to how you must assign an explicit unique numeric value to every item in the ME control list selector. I am writing this value back to the PLC (just like you would do on the 'Connections' tab in ME) by binding the 'Selected value' property to a PLC tag called 'SelectedNum'. You might find this a bit confusion and/or convoluted at first. I did. It took me a while to figure it out. Eventually, you'll see there is more flexibility here compared to the ME control list selector. The 'Combo box' object is very similar. Just as another example, you can create an Enumeration under Model in Optix and tie that to a combo box. Here you see I've done that with an enumeration called CanTypes. I write the value of the selected item to an integer PLC tag called 'CanType'. Thank You, very helpful. Automateshane, what version of Optix are you running? I have 1.2.0.263. It will not let me select object type for (Product1) and change it to my other object with variables (Productconfig). Am I missing something or might there be an issue with the version I am running? Steve, I am currently at beta version 1.3.0.242, but your version should be okay. I did what you are referring to in an earlier release. I am not sure to understand what your problem is, but I will just explain the process I followed. First, I created the ProductConfig object type by right-click of the 'Model' folder and selecting New --> Object. Then, on the properties of this new object I click the + symbol for 'Add new' and select Variable. Repeat this process to add all the variables you need for your product/recipe definition. Note that I added engineering unit information to some of the variables and default values. With this object type definition created, you can then create the master object by adding instances of this subtype. Again right-click on the 'Model' folder and choose New --> Object. I named this object 'Products'. Now you see it listed under the 'Model' folder. You can right-click on it and select New --> ObjectTypes --> and you will see the name of the type previously created (ProductConfig in my example). Using this process you add as many instances as you require and name them accordingly. My application does not require a large array so I did only Product1 thru Product10. Then you can tie the corresponding PLC tags to the variables of each product config instance. This of this kind of like creating a UDT that consists of multiple instances of another UDT. You must create the UDT that is nested before you can add it to the parent UDT. Hope this helps to clarify. AutomateShane I created object(Productconfig)with two variables, then I created object(Product), my issue is that when I right click on that object(Product) I do not see option for new object types, or my previously created object(productconfig) In the list. I only see object. Steve, My apologies, I see now that I've left out a crucial step. The ProductConfig object isn't an instantiable type until you explicity make it so. If you right-click on the ProductConfig object, drill down to Refactor and then select 'Transform instance into type' it will change the single instance object into a type definition from which you can create multiple instances, including embedding them in another object. That should solve it. P.S. - You can easily take a screenshot using the keystroke Windows key + Shift + S. It will freeze the window in its current view and then you can draw a box across the part you want to take a snip of. Then it is automatically on your clipboard and you can use Ctrl + V to paste it. Where do I find refactor, I can not find either refactor or Transform Instance into type. Whichever object you have created that contains all the variables of a given product/recipe configuration, right-click on it. AutomateShane This is what I see with right click on object with two variables. I updated to Beta version 1.3.0.310 to see if I would get the refactor in the list and it is the same as version 1.2. Any ideas why you have it in your selection and I do not? I am using pro version. AutomateShane I figured it out. I had to go to the the option gear at top right and select Factory talk Optis Studio options then select Advanced Mode. Now when I right click on objects with variables I see Refactor. One last thing though, it did not automatically create Displayed value path and Selected value path links. I had to point them to the UDT member then edit the link with {Item}/XXX. If there is something I missed please advise. Interesting, I didn't realize that was hidden as an advanced feature. Glad you figured it out. About the links, that is the correct way. They are not automatically generated. n </s> |
<s>[INST] Two version of RSLogix5000 and one license I have controllers 1756-L56 Rev.15 and 1756-74 Rev.32. I have two activation on workstation. I have to setup another machine with Rockwell software. Is any way I can run RSlogix5000 v15 and Studio5000 v32 with the one license. Somebody told me if I go to FTAM and activate v21 I will be able to open both of them (not the same time) [/INST] Hi Piotr, Yes, One license can activate both version of software ( v16 & v32). You have to use Flexera type of license. For more detail, please refer IN9769 Just to clarify - the license that allows for this are older licenses allowing for Legacy (Flexera) activations. These can be recognized via first digit of serial (1*** or 2***) On the newer licenses provided via Subscription Portal only Studio 5000 Legacy allows for both RSLogix and Studio 5000 activation on 1 license. Filip, The one license serial starts from 2 but another one says n/a. I don't know why? That perticular license have been borrowed, and from my understanding it's borrowed either from your machine or from someone else's. Now, from what I see this license might be able to be reactivated on versions between 20.05 and 26.01 and activate your software on the whole range of RSLogix 5000 and Studio 5000 Logix Designer. The two licenses run on the server I can run remote session from my home and do troubleshooting . The problem is sometimes I don't have access to internet and I have to borrow them. Every time when I do it nobody else can use Rockwell software. I was thinking to buy another license and run another laptop with Rockwell software in case of it but I am wondering if I will be able to run RSLogix5000 v15 and Studio5000 v32 with only one license. The rule of borrowing is the same as in library and it works as intended - if there is only one copy of license and have been taken, nobody else can take it until it is returned. The RSLogix 5000 and Studio 5000 can be activated with 1 license in sense that you want to use multiple versions of the software, but if you want to run them simultaneously or you want to borrow it on the go, you need to have multiples of them so other users can use their software. Thank you for you help What you were told is correct, you just need your serial # and activation key and you can activate any version. n </s> |
<s>[INST] Powerflex 523 and connected components Summary: Connecting to 523 through connected componentsThis may be a simple question but i can seem to make it work. Is here a way to connect to a Powerflex 523 drive through Connected Components Workbench using the USB port on the control module? [/INST] No, the only way to connect live to the drive with CCW is to use the 1203-USB while the drive is powered. However, you can pre-configure you program in CCW, then export the file to a .pf5 format from CCW. Then plug your computer into the drive via the USB port in the back of the control module and import the .pf5 file to the drive. Once this is done, your drive should be programmed and ready for testing. See Chapter 2 of the User Manual; http://literature.rockwellautomation.com/idc/groups/literature/documents/um/520-um001_-en-e.pdf First, thank you very much for responding so quickly. I am not concerned with being live with the drive. I have used the built in configuration software and it does work well. I was just curious if I could do the same thing through CCW. It is good to know that I can export the file from CCW and then use the built in program to import it. Thanks for taking the time to do the screen shots too. Good to know I can get quick, reliable assistance here. I didn't load my screen shots correctly, have a look below; Sorry, I couldn't figure out any other way to load multiple images. n </s> |
<s>[INST] Atlas Copco Combox-e communication I need to connect to a Combox-E device from an ENBT card. I have the combox-e manual and I am confident that I can set up the WHAT (data read and write) that needs to be communicated to the combox-e.The problem is that no-one seems to know HOW the combox-e is supposed to be contacted. Do I add it to the io-tree under the enbt? If so, with what parameters?Or do I MSG it. If so, what type of MSG? Atlas don't seem to know despite specifically mentioning a compactlogix in the manual. [/INST] It's an I/O connection; don't try to run it faster than 100 milliseconds minimum; I would use 250 or 500 ms. Transactions are launched using a data window mechanism.... it's not easy to do. I did a very detailed evaluation of the Combox-E performance last year and decided to not use the ComBox-E but rather change to a ComBox-S with the Modbus Proxy function. The ComBox-S is well understood, well supported, and faster than the ComBox-E. ....ok, thanks. I am assumming I can just make the input assembly large enough to handle the query?the output assembly big enough for a set number of parameters if I want to get more than one at a time?And 0 for the configuration assembly? But what do I put in the 'instances'? I unfortunately don't have a choice in this matter. I also cannot test any code since the thing is already on site.Any extra information yo can provide me with will be much appreciated. Hi Did you get the combox-e to work? I'm about to do the same work and it would be very interesting to know how you solved it. Within the Logix5000 Project tree, I'd set it up as an Generic Ethernet Module using the following CIP identifiers: Input: Assembly Instance = 2 Size = 31 Output:Assembly Instance = 1 Size = 31 Configuration:Assembly Instance = 1 Size = 0 With this setup, the device will connect to your PAC implicitly at user defined RPI. For explicit communications (MSG driven) you will need a little more information about the Atlas Combox; the CIP structure is usually residing within the Electronic Data Sheet file attached to any EtherNet/IP compatible device. Since it was intended (by design) to be used within a Siemens PAC control environment it is not quite straight up EtherNet/IP, you might want to contact the manufacturer and ask to be provided with an EDS file or, at least, with the information required to compile an EDS file yourself using ODVA's EzEds utility. After a long battle with this device and the local Atlas technical rep happening to go to Europe during this time and not getting any joy from the people who actually built it (besides not getting any joy using their own proprietary software when connecting to this device) the outcome was: Atlas Copco South Africa took this product off the market. Summary: Don't try to use this, it doesn't work. Thanks to everyone who commented. Just want to say that all the instance numbers and sizes and MSG setup and what not that you supplied are the same as in the user manual and what the guys from Atlas Copco Europe provided and is just generic information for connecting an ethernet device. Practically, it doesn't work for this device. Dear Experts, Am using L75 Allen Bradley - Controllogix processor and Atlas Copco Power Focus Tool. Am new to work in This Power focus Tool. Both the PLC and Power Focus Tool having a Ethernet Communication . So please Tel me how can i communicate this TOOL to PLC and How can i get datas from tool . Please Help this support. Regards, Arasan.. Have you searched samplecode website ? I found this over there http://search.rockwellautomation.com/search?client=samplecode&oe=UTF-8&ie=UTF-8&output=xml_no_dtd&proxystylesheet=samplecode&site=sample_code&getfields=*&lang=en&hl=en&sort=date:D:L:d1&wc=200&wc_mc=1&ud=1&filter=0&q=atlas%20copco Thanks, Vijay n </s> |
<s>[INST] Factortalk view tag browser Good day everyone. I encountered a problem 2 days ago. My tag browser doesn't come up again when I click to make a connection from an object to it. Any help will be appreciated. The software hangs for over 5 hours and nothing comes up. – / 2 [/INST] Welcome to Engage! Although it could be something wrong in the system, sometimes it happens that the window is just off-screen. If for example you have previously used a second monitor attached to the PC, it could be that the pop-up window for Tag Browser was opened at an X/Y coordinate that now places it off the screen, so it will launch but it will not be visible. To verify if it is the issue, please proceed as follows: Make sure the Tag Browser is in focus, pressing the button to launch it Press the Windows key on your keyboard (and keep it pressed) along with the left OR the right arrow key and the browser window should appear (the arrow key should be pressed multiple times) Hope this helps, fuzzy logic Please don't forget to LIKE and highlight the decisive answer: REPLY > Make Best Answer Hello thank you for the help but do you know any other reason why it could be so ? Because the window and arrow thing didn't work. Thank you. This solved it. – / 1 Thank you for the follow up. Yes, beside the keys combination I suggested to move the Tag Browser windows in the visible area, which works for Windows 7 and Windows 10 (my doubt is that you did not do it correctly - just edited my previous post to better highlight the procedure) you can reset the window position deleting the related registry, which instead requires a better knowledge of the operating system and can create issues if not followed carefully. The technote you posted a screenshot of is pretty old, I suggest to others encountering the same problem to open the following one: BF19830 Please consider that a TechConnect contract is required to access the above technote. fuzzy logic Please don't forget to LIKE and highlight the decisive answer: REPLY > Make Best Answer The fact that this issues still exist in V13 is annoying, of all of the software I use on a daily basis Factorytalk is the only one to have issues with sub windows opening off screen. There have been many changes in Windows in recent years and for the most part it seems the ability to select an off screen window and move has been broken, I have not been able to move an off screen window in Win10 for about a year now. but honestly, it should be a issue anyways. @oluwaseun, about the only solution I have found is to go into your display settings in Windows and move one of the displays (assuming you have multiple) positions around until you find the off screen tag browser. so you open the tag browser see it is off screen press ESC to close it open the display properties move a display to a new position save reopen the tag browser see if it appeared if not repeat.... you might be able to move the display position with the tag browser open but this can cause window focus issues. this is very much a RA problem in that why does it not open at the focus point???? n </s> |
<s>[INST] 5069-IY4 Properties Missing once upgrading I had to install version 33, 34, and 35 so I am not sure what version created this anomaly but now even in V32 when I try to configure the card the thermocouple input ranges are missing. Normally you can select type J, K, etc but the only option is -100mV to 100mV. The option to change the temperature units is missing as well. [/INST] Miller The channel summary shows basic info Go to the individual channel to configure the thermocouple type. I think you have a newer AOP version but try drilling down to the channel level. Welcome to Engage, Tim Miller! Just to confirm what Philip wrote, you can configure your analog channels also within the new AOP, drilling down each channel: fuzzy logic Please don't forget to LIKE and highlight the decisive answer: REPLY > Make Best Answer I completely overlooked the drop down arrow. Thank you. n </s> |
<s>[INST] Converting EAS data into a CSV tag name data base Summary: I need to know how to convert EAS symbol data to a CSV format to create a tag data baseHello, I need to replace an obsolete third party HMI, a Quick Panel Jr.. I have selected an Automation Direct C-More Micro panel which is DF1 ready and is Tag Compatible. In this application the PLC is a SLC5/3 and i can export the symbol data as an EAS ASCII file is RSLogix. But I don't know how to convert the exported data into this CSV tag format for the HMI to import. Can anyone help? [/INST] Browse to EAS file with Excel. Change from All Excel Files to All Files, open. Text import wizard will open. Click next, add comma to delimiters. Should look good after that, you can save as CSV. I attached Word doc with screen shots. n </s> |
<s>[INST] 2711C-T3M file transfer by rs232(db9) Is it possible to upload application file from 2711C-T3M via rs232(db9)? [/INST] Hi @FiveCents and welcome to Engage ! Please note that the Upload feature for PanelView Component is not implemented inside CCW. So basically the answer is: no, it's not possible. There are chances you can do this upload through the onboard USB, following these technotes: QA30874 QA56307 Hope this helps. fuzzy logic Please don't forget to use the LIKE button and highlight the decisive answer : REPLY > Make Best Answer n </s> |
<s>[INST] RSlogix5000 V18.01 - with full toolkit license I installed the V18.01 over V18.00 and since than, it can not find the activation license. Anyone with ideas? ** picture with license number removed ** Ceeya [/INST] I'm not sure I would display my serial number for others...but are you having issues with any of the other packages?? is the activation server running??.. did you replace node locked with concurrent or vice versa? .. Operating system of computer...service pack... all on local machine or spanning across network drives??. I've encountered the same problem with two customers of mine, they was using the old master disc ativations... Tech Support has confirmed there was a problem inside the version posted on the download website, they should recover the issue during this working day (19th of July). Try then to download it again.... :smileysurprised: - fuzzy logic Just to confirm the revised version is available for download ... the revision is now 18.01.01.... - fuzzy logic what update compared to 18.00?any release notes available? Found it! Thanks n </s> |
<s>[INST] SmartGuard 600 1752-L24BBBE, I cannot find a EDS file for this product, also how do you program it, I was told by my rep that I could use RSNetworks for Ethernet/IP to set it up, but unlike the DeviceNet version, I do not have a Logic tab, probably because I cannot find a EDS file, any help would be appreciated, I have talked with my TechConnect rep, and they recommended upgrading RSLinx Classic, so I did to version 2.55, no luck. [/INST] To program and configure the Smartguard 600 Ethernet/IP version, you still need RSNetworx for Devicenet... :smileysurprised: Anyway, you may find informations about needed software are in Aid 61509. See also Aid 56983 , User Manual , Reference Manual , Inst. Instructions for other infos and instructions to use Ethernet connection to access and program the Smarguard 600. Hope this helps… - fuzzy logic n </s> |
<s>[INST] drag and drop from different routines in ver 31 Summary: could drag and drop from different routines prior to rev 31, can't do it anymore in ver 31just upgraded to rev 31 in Studio and have found out that one of my favorite functions which was dragging and dropping tags from one routine to another is not possible. just wondering if it is actually gone or do I possibly have something turned off. Anyone getting the same result [/INST] That functionality is no longer available. What you can do (new to v31) is drag a routine's tab off of the project which creates a separate window. You can then drag and drop between them. This is great if you're back at your desk using dual monitors, but with just you and your laptop sitting in front of a machine, not so great. I'll file this one under Nice try, Rockwell n </s> |
<s>[INST] CS3000 for Windows XP Dear All, Can we access the CS3000 application for Windows XPI have tried to communicate the FlexPak 3000 using via Windows XP butCommunication Error. I have read the CS3000 Manual. CS3000 only require for Windows 3.1, NT and 98. Thanks [/INST] Check to make sure your cabling is correct. I use CS3000 ver 6.14 all the time with FlexPak3000 and GV3000 drives with Windows XP Hi, if RSlinx is running a driver for your serial port, shut it down and retry Does anyone know where I can get CS3000 software? The software should be available from any A-B distributor. Also, any Reliance Electric distributor should be able to supply. Try to see at the following link for CS3000 software download: http://www.reliance.com/prodserv/standriv/d2916.htm edit: updated download link http://www.reliance.com/prodserv/standriv/CS3000.zip - fuzzy logic n </s> |
<s>[INST] 20 COMM D FW VERSION Summary: ERRORS WHEN CHANGING 20 COMM D MODULE WITH DIFFERENT FIRMWARE [/INST] I'm getting some faults related to PORT 5 adapter on a PF70 with device net adapter 20 COMM D, so after troubleshooting it I decided to change 20 COMM D comms adapter, the one that is installed is a 20 COMM D FW VER 1.007 Ser B and I have a new one FW VER 2.001 Ser B, after installing the new one and downloading the config to it a new fault rise and I wasn't able to clear it, the fault was related to config parameters. When I downloaded the config to this new adapter the HIM asked me for confirmation telling that this was a different version to that I hited the enter button accepting the warning. Then after a cuple os seconds of resetting everything the fault appeared. I put again the old module with no faults. Do I need to have the same FW version to replace the 20 COMM D module? Any help will be must welcome. You might simply have to go through the Parameters of the 20-COMM-D and set them the same in the new one as in the old one, by hand. HIM Copycat doesn't work between firmware revisions, as far as I know. You could use the HIM and a piece of paper, or us RSNetworx for DeviceNet software to access the 20-COMM-D parameters. Is not necessary have the same firmware version. Is the fault related to Faults 71-75 Port 1-5 Adapter? n </s> |
<s>[INST] ME Alarm List I have a PV 600 Plus running FT ME. In the alarm list after an alarm is inactive it randomly stays in the alarm list. In Alarm List Properties Display I have both of the Inactive conditions turned off. I have both the Active conditions turned on. Since I have more than one PV I cannot use the acknowledge system built into the PV. I only want to use the alarm system for displaying time stamped alarm messages. Normally it works fine and when an alarm goes inactive it disappears from the list. Randomly it leaves one behind. It all worked fine before I put in filters. They decided they wanted to separate the Temperature alarms from the Mechanical alarm so I have 2 lists. After that it started randomly leaving messages behind. [/INST] Michael, did you see Aid 65951 ? It seems to be the issue you got... There is a new firmware for your PVP, v5.10.03, available for download at the following website: http://support.rockwellautomation.com/ControlFlash/FUW.asp - fuzzy logic n </s> |
<s>[INST] RSView SCADA Bulk Aknowldgement of Alarms In our project, there is two ways of aknowledging alarms, either a Bulk Aknowldgement or individual aknowledgement of alarms.When we do individual acknowledgements of alarms they acknowledgement bit goes through sucessfully to the PLC to the respective alarm block. When we do Bulk aknowledgements of alarms, the aknowledgement works for most of the alarms but not all. What could be causing this problem? In the PLC the acknowledgement Bit does not seem to be registering when we do Bulk Ack of Alarms. [/INST] What HMI are you talking about? RSView32, FTView ME or FTView SE? And how are you triggering this bulk acknowledge? n </s> |
<s>[INST] PanelView 300 Hi everybody, I have a problem with a panleview 300 micro, and I would really appreciate any help with it. The thing is that I recently downloaded an application to this panel and as soon as it finished, it lost the communication. I have been try to communicate with it again but I haven´t had luck. Rslinx does not see it neither. I also tried to download the old application direct from a USB (jumping the RSlinx) unsuccessfully, I proved the cables and connection and everything is fine. It has loaded the new application but shows: Terminal is offline. Does anybody know how can solve this? Or even, how to reset to the default configurations? Because I pushed already the forward and back arrows simultaneously, but it doesn´t restart. Any help I´d really appreciate it. Thanks [/INST] May you please post the catalogue number of your Panelview ? Any error codes other than the message you got ? - fuzzy logic Hi fuzzy logic, the cat number is: 2711-M3A18L1, and when it loads shows: 686 Panel offline, when I push the arrows trying to reset the configuration shows: Error 31. That is all that displays. Thanks I have a similar problem with my panelview 300 (2711-K3A14L1). I can download a program without problem but when I try to fit the panelview with the micrologix 1200 I got the same error, anyone can help? Well, error 686 is a communication error (loss of communication) : 1. Check cable connections and DF1 setup in the PV and the PLC. 2. Wire up the hardware handshaking lines and enable handshaking in the terminal. See User Manual for connections.See Aid 57313 for cables. See Aid 42387 about error 31. - fuzzy logic Hi, I checked the cables, however, I can not access to the configuration display, I can´t set anything in the terminal.Is there any way to reset it? Check your application... sounds like your allready using the arrow keys in it. To reset the PV300, PV300 Micro, PV550 (keypad, keypad & touch) or the PV600 (keypad, keypad & touch):Simultaneously press the Left arrow , Right arrow , and Enter ↵ keys. The terminal performs its powerup sequence.•If you press the Left and Right arrow keys before the Enter ↵ key, the Configuration Mode menu appears.•If the Left or Right arrow keys on the PanelView 300 Micro are assigned as function keys, you must use the GoTo Configuration Screen button.If you press the Enter ↵ key before the arrow keys, the terminal runs the loaded application.•The sequence in which keys are pressed (while running an application), determines what appears after the reset. n </s> |
<s>[INST] GuardPLC 1600 with 1734 Point I/O over Ethernet IP I am trying to get work 2 OB8 Point I/O cards working with GuardPLC. I can scan the first card, but can not the 2nd On the configuration with OB4 cards two of them are working fine - this is confirmed by Rockwell Support - they haven't OB8 on stock to test it. Has anyone tryied to configure 2 OB8 modules and have them working? The Connection status on Ethernet/IP shows status connection time out to the OB8 module. The Chasis size is OK. GuardPLC scanner shows data receiving and send to 1st card. Data from 2nd card is reveived, but nothing is send into it. Regards, Pawel [/INST] nan n </s> |